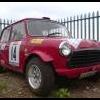
Weber Bulkhead Box
Started by
TopCatCustom
, Apr 12 2011 07:34 AM
8 replies to this topic
#1
Posted 12 April 2011 - 07:34 AM
Given that technically chopping an air box into the bulkhead is modifying the monocoque and may need IVA etc etc etc, (does not concern me at the mo), is there any reason why these air boxes have to be made out of steel? If it's a modification then it's a modification- whether made of titanium or cardboard.
I'd rather make one in ally, it is not load bearing or carrying shocks, and even a seam welded steel box with an open end is technically flimsy- so I cant see why they have to be steel! Ally, pop riveted and bonded in should be ok shouldn't it?
I'd rather make one in ally, it is not load bearing or carrying shocks, and even a seam welded steel box with an open end is technically flimsy- so I cant see why they have to be steel! Ally, pop riveted and bonded in should be ok shouldn't it?
#2
Posted 12 April 2011 - 07:55 AM
I would have that as anything within 12" of a suspension mount is considered structural (in an MOT at least) a bulkhead box would have to be steel and have to be welded in.
If you've got a crazy strong weld in cage then it probably wouldn't matter but even them I can't imagine anyone being happy about a FG box being riveted to your bulkhead.
If you've got a crazy strong weld in cage then it probably wouldn't matter but even them I can't imagine anyone being happy about a FG box being riveted to your bulkhead.
#3
Posted 12 April 2011 - 08:05 AM
It is a full weld in cage so will be very strong, and only a single weber box not a split type so I doubt it would be in 12" radius of a subframe mount? And ally not FG
#4
Posted 12 April 2011 - 09:04 AM
Grab a tape measure and go in 12" from the top of the front subframe tower bolts, it's probably closer to the area you'd fit a bulkhead box in than you'd think.
If it's only a singe webber box then I'd imagine you'll be OK but it's always worth checking.
If it's only a singe webber box then I'd imagine you'll be OK but it's always worth checking.
#5
Posted 12 April 2011 - 06:52 PM
I recently asked my mot tester about a bulkhead box for a turbo conversion on my mini and his reply was "if its seam welded and made from the same material its fine" he also added "its like repairing the seals or anything else on a cars body work, if its done right it's all gravy"
But he also didn't mind that my boot floor in my land rover discovery was bonded in with windscreen glue
But he also didn't mind that my boot floor in my land rover discovery was bonded in with windscreen glue

#6
Posted 12 April 2011 - 08:55 PM
The objective is to carry any shear structural loads across the bulkhead. The way to best do this if a large rectangular hole is to be cut in the bulkhead sherar panel is to weld a substantial steel edge around the rectangular hole.
I would suggest that a continuous 3 mm steel strip about 30 mm wide all round would more than carry the loads adequately so long as it is plug-welded through 6 mm dia holes spaced at about 30 mm at half the strip width, plus a tack weld also every 30 mm at half hole pitch. Then grind back and paint. If an aluminium box were then fitted into the rectangular hole and bolted in place with suitable sealant using, say, about 12 bolts of about M5 size, again spaced equally around the edge that would be fine.
Any weakness caused by the hole could only be a reduction in shear strength and the welded edge strip would more than replace this in terms of shear strength.
I know my MoT tester would be entirely happy with this.
Even with asteel box welded in, the load is still only resolved around the edge of the original hole by the overlap of the flange of the box.
I would suggest that a continuous 3 mm steel strip about 30 mm wide all round would more than carry the loads adequately so long as it is plug-welded through 6 mm dia holes spaced at about 30 mm at half the strip width, plus a tack weld also every 30 mm at half hole pitch. Then grind back and paint. If an aluminium box were then fitted into the rectangular hole and bolted in place with suitable sealant using, say, about 12 bolts of about M5 size, again spaced equally around the edge that would be fine.
Any weakness caused by the hole could only be a reduction in shear strength and the welded edge strip would more than replace this in terms of shear strength.
I know my MoT tester would be entirely happy with this.
Even with asteel box welded in, the load is still only resolved around the edge of the original hole by the overlap of the flange of the box.
#7
Posted 12 April 2011 - 09:08 PM
i have seen many a rally mini with a ally weber box pop - riveted in:) but steel ones are strong and dont weigh much at all, mine fited in 1 hour and weighed the same as the scrap metal i cut off:)
#8
Posted 12 April 2011 - 09:27 PM
So long as the screen lower rail is not rusty and is firmly welded in and the bulkhead cross member box section is correct, then any shear loading in the upper bulkhead will be very low indeed, even in a crash case. However, with the current regulations in respect of unaltered structure, then if what I suggest above is done, there can really be no objection, even if an inspection is required.
#9
Posted 13 April 2011 - 07:37 AM
Thanks guys, I may weld a strip around the edge as Cooperman suggests then, or even fold up some 3mm strip to make angle so the ally box doesn't have to have returns on the face to be bolted in, if that makes sense.
1 user(s) are reading this topic
0 members, 1 guests, 0 anonymous users