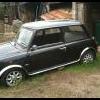
Do I Need A Torque Wrench
#61
Posted 21 January 2011 - 09:16 AM
#62
Posted 21 January 2011 - 09:26 AM
Even a £10 ebay special will be better than no torque wrench. £50 will get you a good'n - with a test certificate.
Having callibrated a few torque wrenches I would argue that this is NOT true. My old cheap wrenchcould not be callibrated through the whole range, you could get 50lb right, but everything else would be out. The consistency of the thing was useless too, +/-5lb at best.
For those with a torque wrench, always slacken it off after use so that the springs are not stored under load. this tends to thow them out eventually.
#63
Posted 21 January 2011 - 11:04 AM
Evne good torque wrenches have their limitations...... ie don't use them below the 1st and above last 20% of their scale...... as they tend to lose repeatability at these points, that is why one torque wrench simply would never be enough, a range is required, I have 5 different torque wrenches with a reasonable overlap on each.....
To do a hub nut you need one that starts at about 100 lbf ft and goes up to 250 lbf ft ..... Norbar do some pretty good ones, as do Britool, Snap-on, Mac etc...... Always try to get a "professional" range tool.
And definately NEVER use to undo and do as Wil h above, always release the spring

#64
Posted 21 January 2011 - 11:54 AM
And definately NEVER use to undo and do as Wil h above, always release the spring
Ideally spend £10 on a 1/2" drive breaker bar.
#65
Posted 21 January 2011 - 11:59 AM
#66
Posted 21 January 2011 - 12:08 PM
Interestingly, when I callibrated my wrench I checked it at 20Nm (the gauge only reads down to 40Nm) and it was spot on and repeatable.
As far as I am concerned the crank, rod and head nuts are critical for the use of a torque wrench and I have callibrated my wrence so that it is good at these ranges at the sacrifice of the higher end of the scale.
I do use it for everything else (including wheels, mainly to prevent OVERtightening) but somewhere close is acceptable on general fittings, and experience tells me what is good and bad.
#67
Posted 21 January 2011 - 12:10 PM
For the most part what we are trying to acheive is an even loading on the fixing, with an tension on the fixing that falls between the design guidelines, now mostly this would be in the elastic portion of the fixing.
Some fixings are torqued to the Plastic region, ie stretch fixings, which are also throwaway fixings, some cylinder heads use these and they must be replaced each time they are released.
I wonder how many head gaskets etc fail prematurely due to the lack of use of a torque wrench......
How many times have we heard "I am not taking my car back there again, it only lasted a week" and so these people merrily carry on not using a torque wrench etc...... and what do these same people say when asked ? "never had one fail guv"
#68
Posted 21 January 2011 - 12:23 PM

which is actually a better design for accuracy, but i wouldn't rule out others, unless they're really just toys.
Mini sized fasteners are likely to have torque values that are about 50% of yield. Even if you're tightening a good quality bolt with a good quality torque wrench you'll do well to get the preload to within 25% accuracy, if it's threaded into cast iron or aluminium it's going to give more variable results.
Was the original question about flange to disc fastenings

Remember they went from 1/4" countersunk screws to 3/8" bolts from 7.5 to 8.4 discs, albeit with a reduced PCD.
#69
Posted 21 January 2011 - 12:27 PM
If you need to ask, then you need to use one, I personally need to use one 99% of the time, rather be safe than sorry!
If you want to replace things whilst you've got the thing apart, then check ball joints for wear first before taking things apart, you could re-build the whole front suspension if you have the time and cash?
I'd check ball joints, track rod ends, bolts, and bearings as a min, and reaplace anything that's worn. but that's just me. If this is your daily drive and you need it back on the road over the weekend, I'd just do the discs and pads, maybe replace the caliper pistons and anything obviously worn, that would take me a weekend of work, cup of tea, cig, work, clean things and repeat. then bleed and test brakes.
If you're not confident in doing this then take your time and ask for advice, hopefully people will be nice and not just put you down for wanting to learn. I hope.
Meh.
#70
Posted 21 January 2011 - 02:28 PM
Remember they went from 1/4" countersunk screws to 3/8" bolts from 7.5 to 8.4 discs, albeit with a reduced PCD.
However the screws are simply a retainer to keep the disc in place and are not a primary fixing..... however on the 8.4" system the bolts are of prime importance and are much more likely to cause concern
#71
Posted 21 January 2011 - 02:35 PM
its best to but if you dont have one using tip ex as a marker just count the amount of turns you make to get it of and then repeat it when putting it on.
but then again thers a 2nd hand torque wrench in the classifieds under tools so may as well invest now as you dont want to bey forever using the crude method of just counting the turns.
#72
Posted 21 January 2011 - 02:42 PM
count the times you turn the nut
its best to but if you dont have one using tip ex as a marker just count the amount of turns you make to get it of and then repeat it when putting it on.
but then again thers a 2nd hand torque wrench in the classifieds under tools so may as well invest now as you dont want to bey forever using the crude method of just counting the turns.
How does this help ?
#73
Posted 21 January 2011 - 03:56 PM
7.5 discs do have the wheel studs as well as the disc screws, but the clearances are bigger and there's a couple of extra surfaces if friction is keeping everything secure, not to mention the additional loading/unloading of going round corners, yet the disc screws seem not to bend or shear even though BMC never insisted everyone got ******* about wheel nut torque - not to mention alloy wheels using tube nuts.
#74
Posted 21 January 2011 - 05:25 PM
A pair of new disk CV joints I recently fitted from minispares actually had a 35mm-castle nutIf you replace the castle nut there is a risk of being supplied one that you don't have a socket for. There are two types, 1 & 5/16" and 34mm, both with the same thread and both were used interchangeably by Rover. Ideally if you intend servicing Minis you need both sizes of socket but if you have only the one that currently fits your car and you receive the wrong nut from the supplier you might get a bit stuck.

Edited by 1984mini25, 21 January 2011 - 06:24 PM.
#75
Posted 21 January 2011 - 06:17 PM

What can happen..... when we manufacturers place orders for metals, say for instance 1 5/16" the guy on the phone looks down his list of metric and thinks 1 5/16" hex is almost the same as 35mm as we have that in stock I'll send it out, after all it's only a little bit different.
I often have to send bar stock back because they have supplied the wrong size, frustrating in the least, and I know we are not the only company that has the same problems with suppliers.... and don't even start on material grades

So I am not surprised that this happens, for 11/16" over the last 2 years I have had 6 deliveries of 17mm nearly half a millimeter smaller


1 user(s) are reading this topic
0 members, 1 guests, 0 anonymous users