Hoping to get the block to the rebore company at the weekend now that I have my pistons. The block is quite clean, as I degreased it before stripping it all down.
I asked the rebore fellas how they clean it, they have a parts washer sort of set up. But after reading on here, a load of folk have them dipped.
Im wondering how to clean it nicely, should it be dipped before or after? What actually is dipping, does it eat away at metal like causic might?
Also whilst Im posting, what sort of money are people paying to have new camshaft bearings fitted.
Cheers
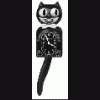
Cleaning A Bare Block
Started by
mini670
, Dec 16 2010 08:03 PM
4 replies to this topic
#1
Posted 16 December 2010 - 08:03 PM
#2
Posted 16 December 2010 - 10:20 PM
parts wash, re bore and if you can find someone with one big enough get it in an ultrasonic cleaner
forgot to say wash again after the bore. its amazing how much you can get out with an ultrasonic cleaner, even something that's been through a wash a couple of times.
forgot to say wash again after the bore. its amazing how much you can get out with an ultrasonic cleaner, even something that's been through a wash a couple of times.
Edited by ANON, 17 December 2010 - 12:23 AM.
#3
Posted 17 December 2010 - 12:05 AM
What I do is this:
Get the bored block back from boring and clean it with Jizer then hose it out with a presuure washer and dry it with compressed air. Then I do the 'trial build', measure the deck to piston height and take it to pieces and return the block for machining the deck to bring the pistons to the deck level. A trial build is vital if you want a good engine. That's why some engine builders are cheaper - they don't do all the required operations to build a 'proper' engine. I use linished-down gudgeon pins for the trial build and have the rings off the pistons as you can check all the ring gaps at this stage as well.
Then, when it comes back again, Jizer and pressure wash, making sure the oil galleries are very clean (before fitting the oil gallery core plugs). Blow all the water off with an air gun and dry it. Then wash the entire block and all parts with Brake & Clutch Cleaner and blow it dry again. The outside of the block can then be painted. When the paint is dry lightly spray the inside of the block with WD40 or similar.
Now the assembly can be started properly.
At the machine shop I use I sometimes do the trial build there as they can then do the 'decking' the same day and I can save a trip back.
The final thing is to do the compression ratio measurements and calculations and take the head for final skimming before assembly onto the block. In fact, once you know the pistons will come to the block top, you can measure the combustion chamber volume and take the head for skimming at the same time as the decking.
Good luck with the re-build.
Get the bored block back from boring and clean it with Jizer then hose it out with a presuure washer and dry it with compressed air. Then I do the 'trial build', measure the deck to piston height and take it to pieces and return the block for machining the deck to bring the pistons to the deck level. A trial build is vital if you want a good engine. That's why some engine builders are cheaper - they don't do all the required operations to build a 'proper' engine. I use linished-down gudgeon pins for the trial build and have the rings off the pistons as you can check all the ring gaps at this stage as well.
Then, when it comes back again, Jizer and pressure wash, making sure the oil galleries are very clean (before fitting the oil gallery core plugs). Blow all the water off with an air gun and dry it. Then wash the entire block and all parts with Brake & Clutch Cleaner and blow it dry again. The outside of the block can then be painted. When the paint is dry lightly spray the inside of the block with WD40 or similar.
Now the assembly can be started properly.
At the machine shop I use I sometimes do the trial build there as they can then do the 'decking' the same day and I can save a trip back.
The final thing is to do the compression ratio measurements and calculations and take the head for final skimming before assembly onto the block. In fact, once you know the pistons will come to the block top, you can measure the combustion chamber volume and take the head for skimming at the same time as the decking.
Good luck with the re-build.
#4
Posted 17 December 2010 - 07:36 PM
Cheers guys,
The block is now with the rebore guys. Its having 0.02" rebore, and new cam bearings installed.
Whilst I was there is noticed they use a revolving steamer, which they will use once machining in complete. Outside they had a steam pressure washer. I might ask them if they will do my gearbox for me then pop it in the steam clean machine.
Convincing my Dad that pressure washing the block in his garden may take some time, but ill keep trying.
I forgot to buy some oversize bearings for the crank, so ill have to get those ordered before regrinding. Once everything is there, the trial build can begin.
Sorry to keep asking these questions, just want it to be right after I chucked a fair sum of cash at it.
The block is now with the rebore guys. Its having 0.02" rebore, and new cam bearings installed.
Whilst I was there is noticed they use a revolving steamer, which they will use once machining in complete. Outside they had a steam pressure washer. I might ask them if they will do my gearbox for me then pop it in the steam clean machine.
Convincing my Dad that pressure washing the block in his garden may take some time, but ill keep trying.
I forgot to buy some oversize bearings for the crank, so ill have to get those ordered before regrinding. Once everything is there, the trial build can begin.
Sorry to keep asking these questions, just want it to be right after I chucked a fair sum of cash at it.
#5
Posted 17 December 2010 - 09:27 PM
Ask as much as you like to. We are all happy to help you to build a really good engine and make another great little Mini better still.
1 user(s) are reading this topic
0 members, 1 guests, 0 anonymous users