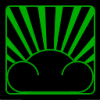
My Poor Wee Mini Sky
#31
Posted 17 December 2010 - 11:54 PM
Chris
#32
Posted 18 December 2010 - 09:39 AM

#33
Posted 18 December 2010 - 02:25 PM
Well despite being -4 outside I tried to put my first patch on the driver's side front inner wing at the lower front. I thought that nobody sees it and it is of little structural importance.

It took two hours to make this tiny patch! I hope I can get faster. If not, I'll not finish till 2020. Tacked it in.

I stupidly cut too far into the inner wing with the cutting disc and then had to blob this in with weld. You'll notice I didn't say weld over it!

And the back - it's a good thing the photo is blurred.

Then ground it down.

I've very mixed feelings. Still hate welding. I could have done it worse - two weeks ago I could have burned holes the whole way along. But I could have done it better - it is ugly and the penetration is not nearly as good as I would have liked. It is so much more difficult welding down on the ground instead of at workbench level.
But I've done my first tiny repair. I should go back outside but its so cold and it goes for my old bladder.
Hugh
#34
Posted 18 December 2010 - 07:44 PM
Graham
#35
Posted 18 December 2010 - 08:14 PM
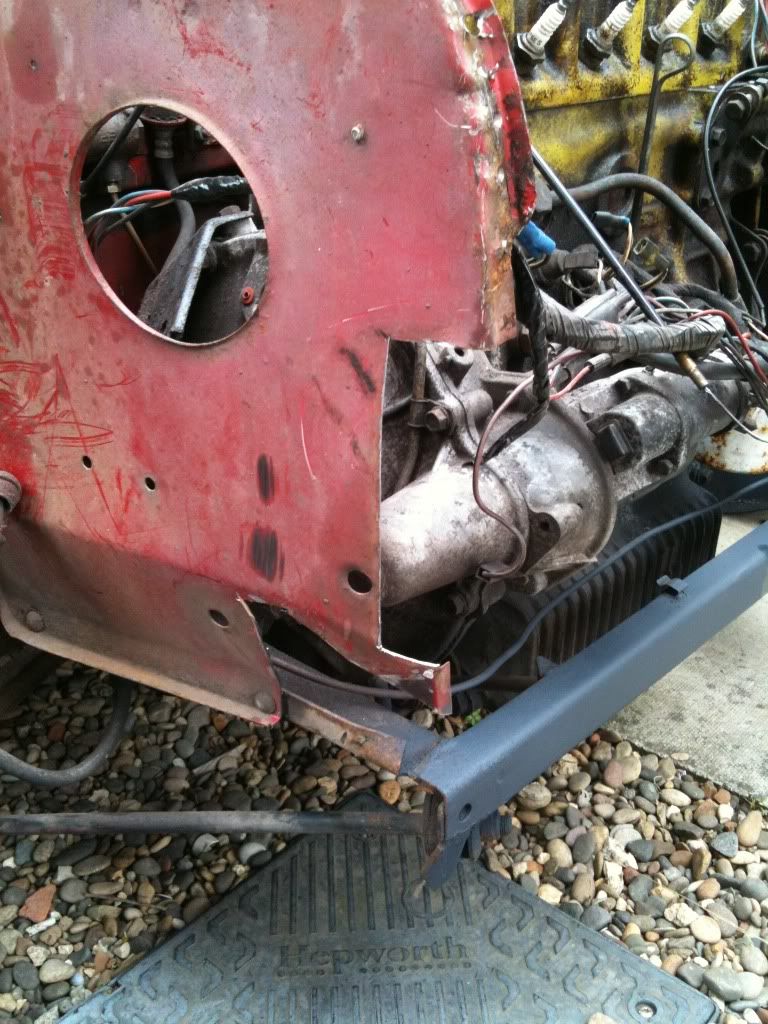
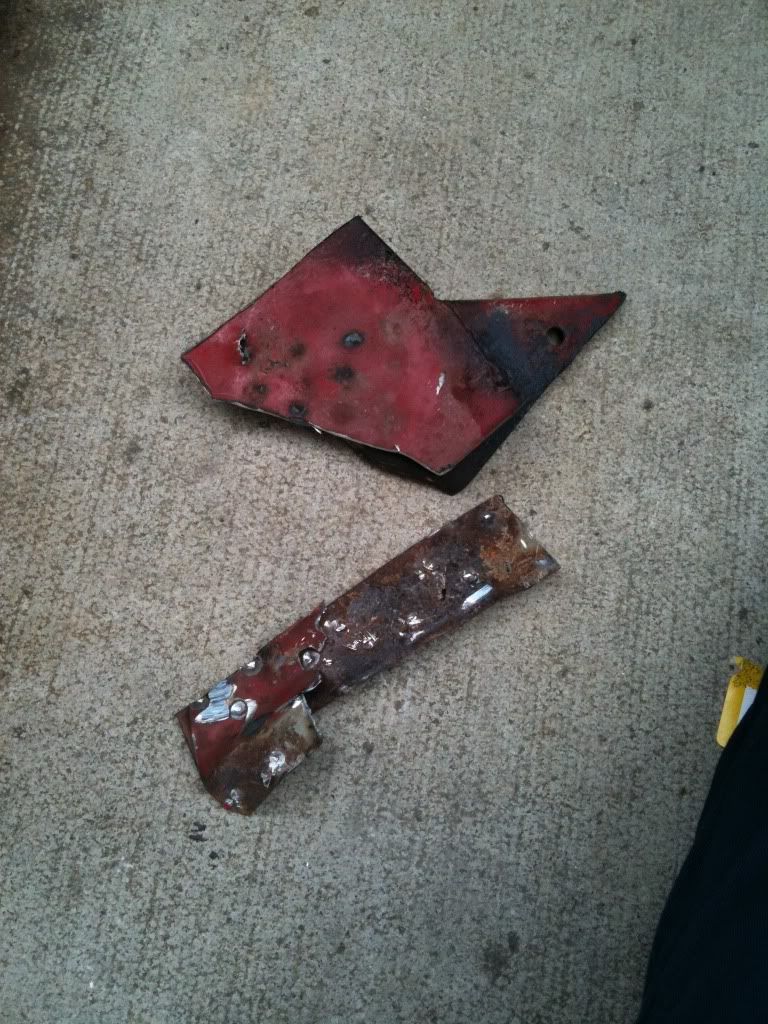
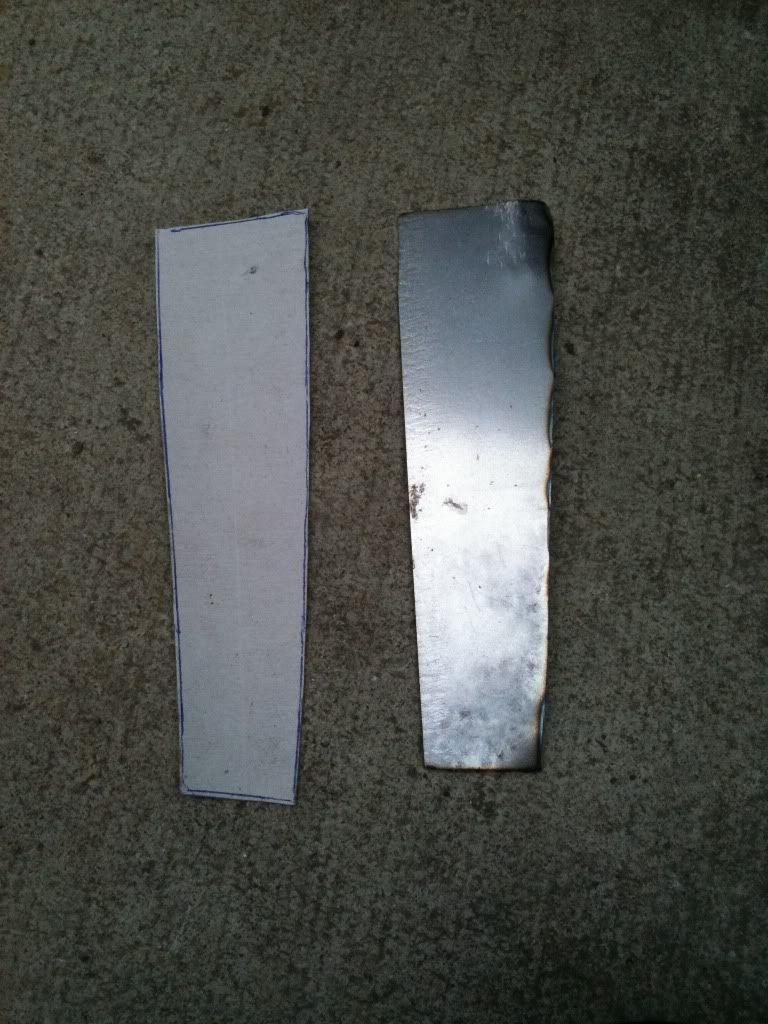
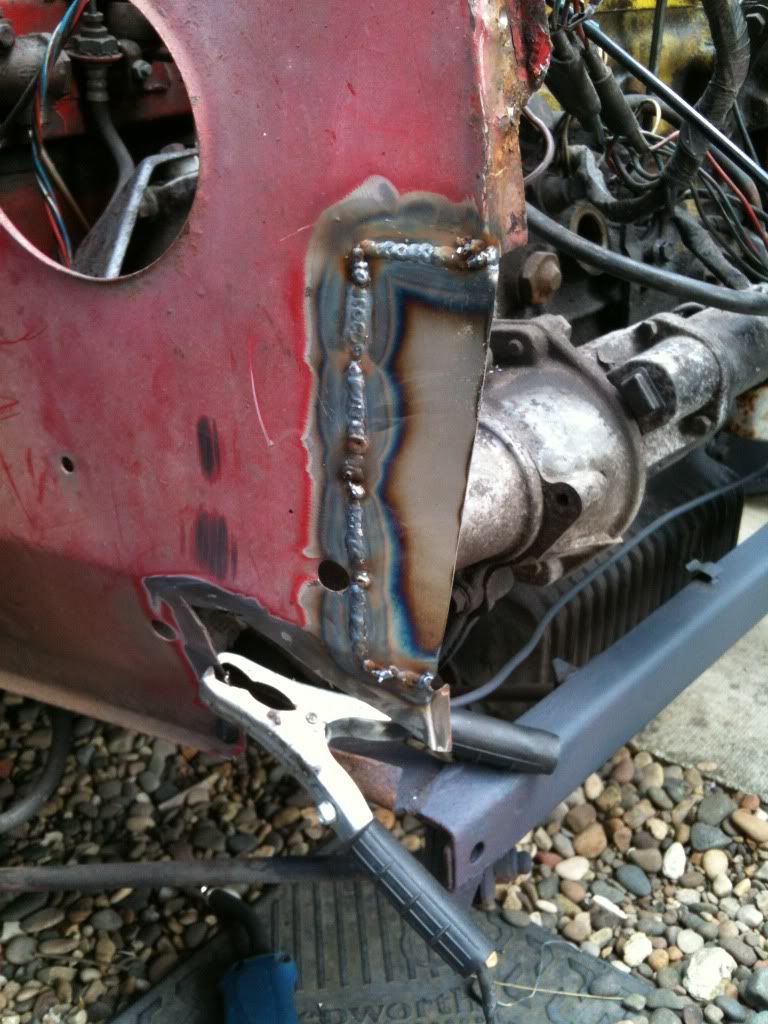
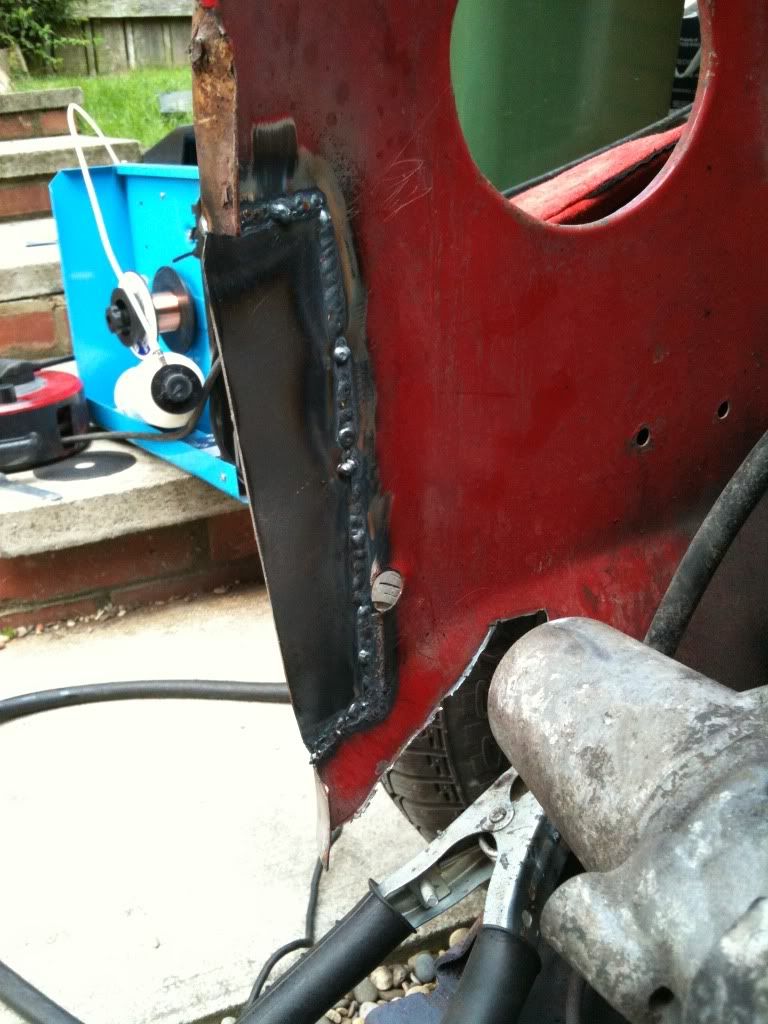
I only welded one side the penetration was brilliant and is now a loverly invisable repair.
Dan.
#36
Posted 18 December 2010 - 08:34 PM
You could have done that in one panel and keep the lip there, welding looks good though Dan, well done
Dan.
#37
Posted 18 December 2010 - 10:03 PM
Thanks Dan. I hang my head in shame. Your repair is beautiful.
Hugh
#38
Posted 19 December 2010 - 01:50 AM
About what mine started out like, Just keep at it you will get it, building skills you can use later!
Chris
#39
Posted 27 December 2010 - 01:45 PM
A good Christmas to you all - notice the wee bit of holly edited into the first picture!
The temperature is above 0 today, just, so I went out to the garage. Stripped out the dash. It seems to be made from cardboard, bits of polystyrene and bits of foam. It really is a bit nasty. The lower dash-rail cover is broken as explained earlier the top one seems fine.

And the rust is really starting to show.



The area round the windscreen is going to take some work.
Hugh
#40
Posted 28 December 2010 - 04:08 PM

I'm guessing you may be buying a whole new upper dash piece? I noticed the edges adjacent to the top dash padding was pulled out likely for access to the padded dash bolts. The rust doesn't appear too extensive which is good as you should still have a fairly decent basis for patterning the replacements.
Chris
#41
Posted 28 December 2010 - 05:18 PM
#42
Posted 28 December 2010 - 05:23 PM
I had a most discouraging day.
I thought I would patch the bottom of the passenger side inner wing at the front. I thought it would be easier having done the drivers side. No it wasn't. It took two goes - 5 hours work!
I meant to record this so diligently for the Mini Forum.
So cut out the rot.

Made a nice wee patch

Tacked it in place

And then did some awful welding.

When I ground it back there were holes which I then tried to fill with weld. That was a disaster. I had ground too far and was trying to weld steel foil! I gave up with the camera. In fact I wanted to give up altogether. But, bravely, I cut more out and welded in a bigger patch. The patch wasn't nearly as nice as the one above.
I then practiced vertical and horizontal welding on some scrap pieces. I needed to up the wire speed. So tried welding in again.

It doesn't look good but it did penetrate a bit better.

Its kind of gloopy in places as my patch didn't fit so well. I had to build up the weld to fill the gaps. After a bit of grinding -

A bit of a waste of a day really. I had meant to get started removing the sound deadening from the floor.
Hugh
Edited by hughJ, 28 December 2010 - 05:27 PM.
#43
Posted 28 December 2010 - 05:32 PM

#44
Posted 28 December 2010 - 05:34 PM
When doing stuff like that I 'pulse' weld, ie not try and do a long run. Weld 5-10mm and then stop, wait till the glow just disappears from the bit you've just welded and then start up again.
Its basically like doing a series of long tacks, stops the panel from warping and also stops you 'blowing' through with the welder.
Long uninterupted runs of weld look good on American hot-chopper but aren't really suitable for the kind of rusty crap you find on a mini.
The welds are flatter, you can hold the torch in one position longer and get more penetration.
#45
Posted 28 December 2010 - 07:19 PM
Thanks for the kind words malcs_miniturbo and megamini_jb.
Hugh
3 user(s) are reading this topic
0 members, 2 guests, 0 anonymous users
-
Bing (1)