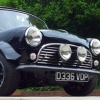
Shock Absorber Mount Repair
#16
Posted 14 September 2010 - 10:19 PM
#17
Posted 14 September 2010 - 10:38 PM
I might try and get an old panel from a scrappers or something to cut some thinner patches out of to go over the thicker bottom patch.
#18
Posted 15 September 2010 - 06:26 PM

#19
Posted 15 September 2010 - 07:51 PM
If you're going to use captives like Pete suggested, the blocks of metal which are threaded are only held on to the inner wings with a few slugs of weld, if you can break them they will come clean off.Getting a drill in will be the main problem really. I'll see how I go anyway.
I might try and get an old panel from a scrappers or something to cut some thinner patches out of to go over the thicker bottom patch.
#20
Posted 16 September 2010 - 11:33 AM
I've managed to sort of the broken bolts pretty much. I used a punch and a mallet and hammered the punch through into the broken bolt. This has pushed the stud back and broken the top of the threaded block away from the inner wing. Once i've got inner wing cut out i'll be able to knock the bottom of it off and I can then use a nut and bolt to hold the top of the shock mount on.
Anyway i've started cutting, its going ok.
I'm just wondering what people think I should do here. Should I carry on all the way down the inner wing (Like i've drawn on in red below) or should I try and get the grinder in and cut along between the 2 lines i've cut so far, just below the bolt holes but above where the panel end before the subframe?
I can't see a problem with cutting all the way down, i'd just need to bend a lip onto the patch i'm going to make right?
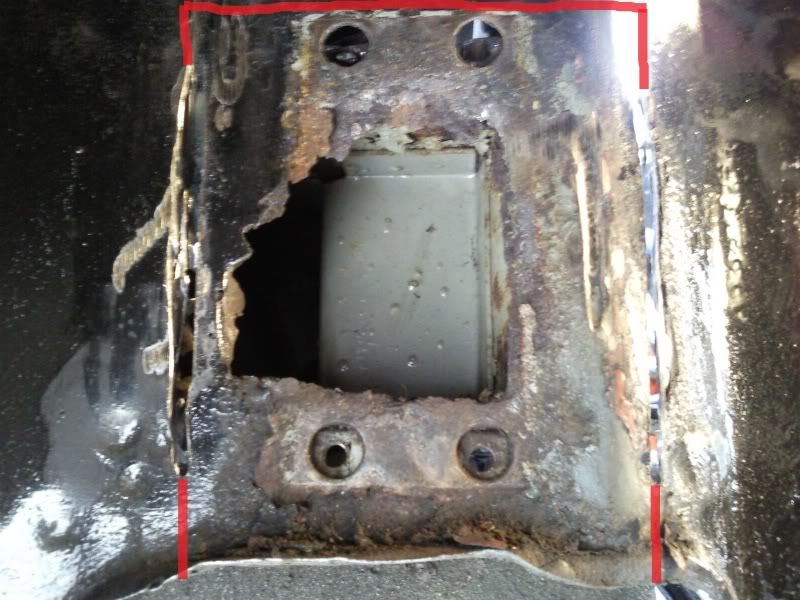
What do people reckon?
#21
Posted 16 September 2010 - 05:30 PM
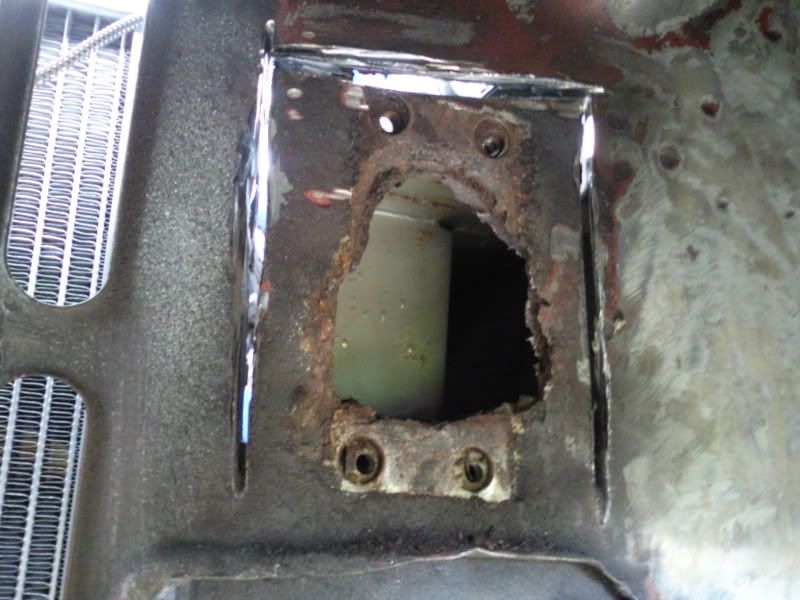
So I think I will just cut all the way down the panel. Then i'll need to cut through the welds on the inside of the inner wing to release this piece from the end of the box section. As far as I can see thats all that holds the inner wing to this area.
Still wondering whether or not to get one thick patch welded in or 2 thinner ones. I'm thinking what i'll do is make up one thicker repair patch which will give most of the strength - Bend this to shape, put a lip on the bottom of it and drill the holes for the shock mount in it; then get that welded in. Then I think i'll get a wider patch made of some thin stuff (maybe something like 0.9mm) and have that welded over the top - overlapping onto the rest of the inner wing and seam welded all the way round.
#22
Posted 16 September 2010 - 05:37 PM
This is being fussy but also the best way to get an original finish but its entirely up to you.
#23
Posted 16 September 2010 - 05:52 PM
What holds the 2 layers together? Or is it just the shock mount bolts that clamp the 2 together?
I was just thinking of drilling some extra holes into the top repair patch so the welder could plug weld the 2 layers together.
I'll cut all the way down and remove the old metal for now. Clean up round the opening I'll be left with and decide what the next step is and i'll see how good I am at making up a repair patch as its going to have to be curved with the shape of the inner wing, and have a lip along the bottom.
#24
Posted 16 September 2010 - 06:01 PM
#25
Posted 16 September 2010 - 06:31 PM
Lee
#26
Posted 16 September 2010 - 06:53 PM
When I think of a 2 layer repair I was thinking similar to what you hard on your car in your project thread:
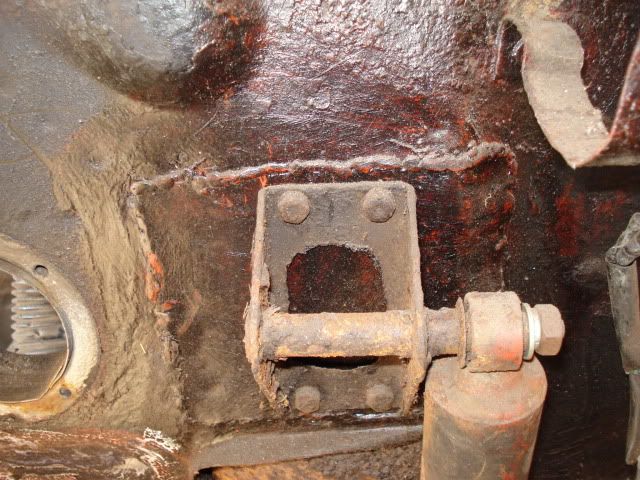
Obviously its better to get it all flush, but i'll have to see how my patch making goes.
I'll get back to you lee about some metal if I need it.
Edited by mike., 16 September 2010 - 06:54 PM.
#27
Posted 16 September 2010 - 07:05 PM
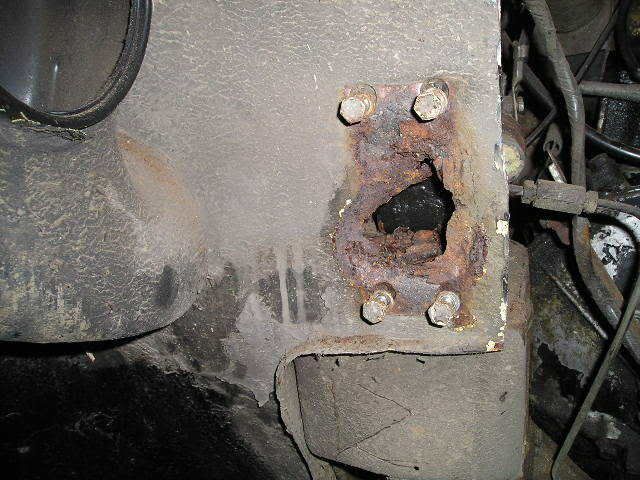
cut out the rot but left the mounting holes, I cut a repair patch out of 3mm
sheet and drilled 4 holes, welded it over the hole and used longer bolts to
secure the bracket,
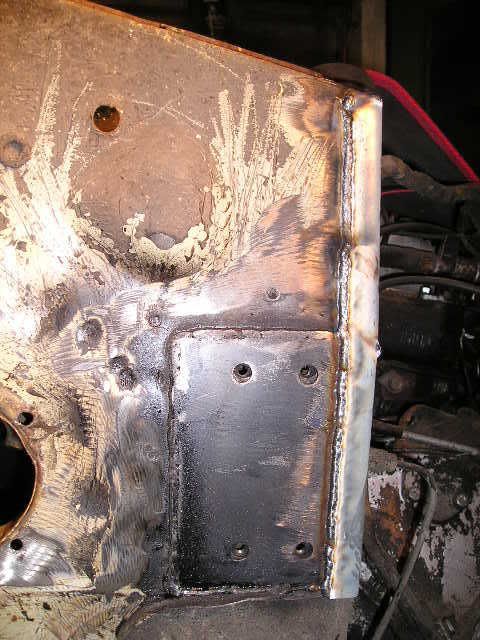
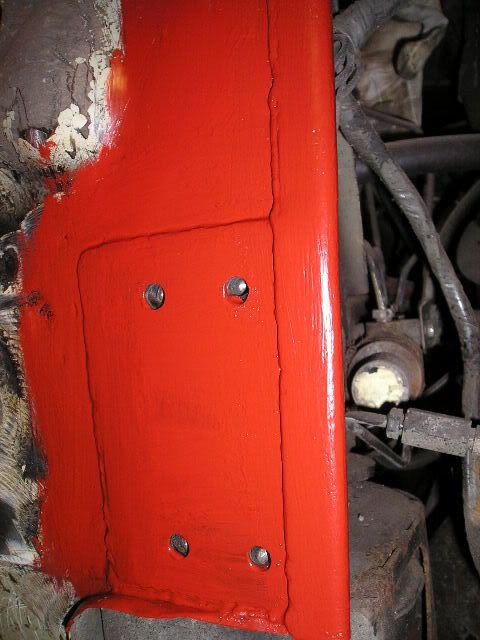
good idea to seal behind the bracket before bolting up to reduce the
risk of water being trapped between the bracket and body..
I also strengthend the shocker mounts..
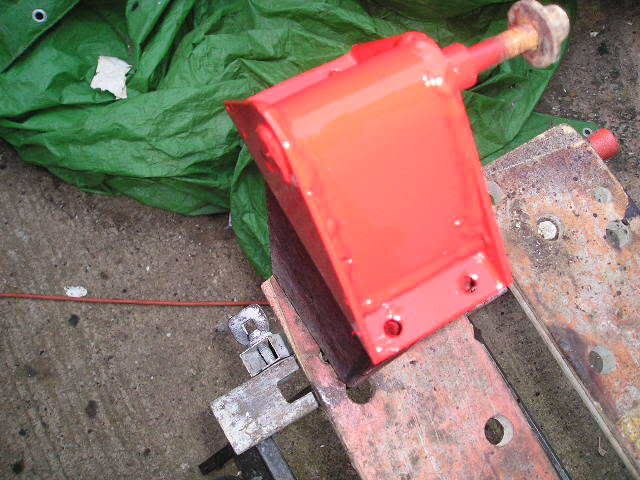
Edited by camp freddy, 16 September 2010 - 07:07 PM.
#28
Posted 16 September 2010 - 07:06 PM
the blocks of metal which are threaded are only held on to the inner wings with a few slugs of weld, if you can break them they will come clean off.
ive done this myself a few times, normally the bottom ones tend to fall off anyways after a few years, but the top ones are abit of a pain, but if you can get a dremmel or something similar, the welds that hold them on will be easy to cut through, just take your time and have lots of patience!
#29
Posted 16 September 2010 - 07:09 PM
Just had a quick look at your thread.
When I think of a 2 layer repair I was thinking similar to what you hard on your car in your project thread:
Obviously its better to get it all flush, but i'll have to see how my patch making goes.
I'll get back to you lee about some metal if I need it.
Seeing that old repair sends a shiver up my spine, what a mess but if you want to do the repair that way (there was just a hole behind that plus they refitted that old mount again, bloody shocking!!) then as long as you have got the other plate behind it that will work fine. There is absolutely none of his scabby welding left on the car, alot of it had not even penetrated properly. Bloody dangerous especially if my boy had had the misfortune to have an accident in the car.
Edited by sonikk4, 16 September 2010 - 07:10 PM.
#30
Posted 18 September 2010 - 11:25 AM

I cut all the way down and started prising the rot off the car, breaking the spot welds etc.
I've cut off the big chunk of rot that I cut around. The only bit thats left now is still double skinned and is held on with the 3 or 4 lines of weld onto the triangle piece on the bulkhead and maybe some spot welds to the end of the box section.
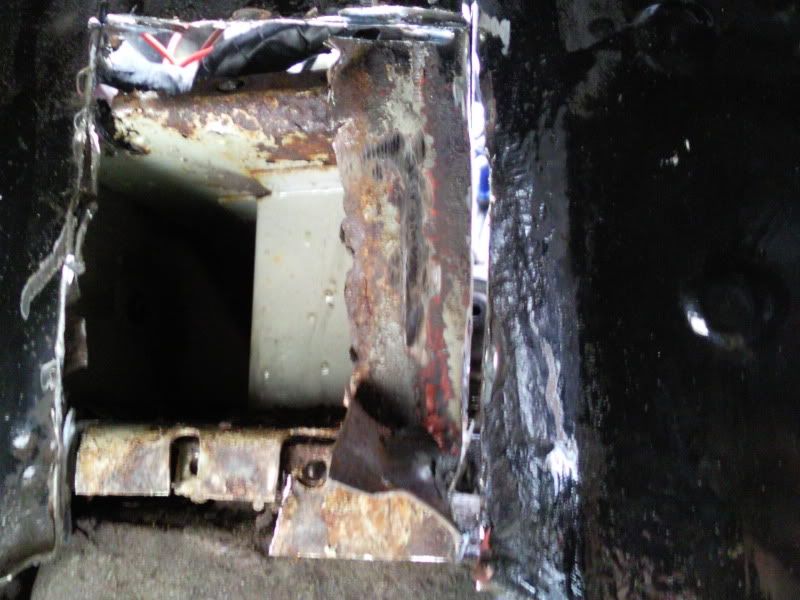
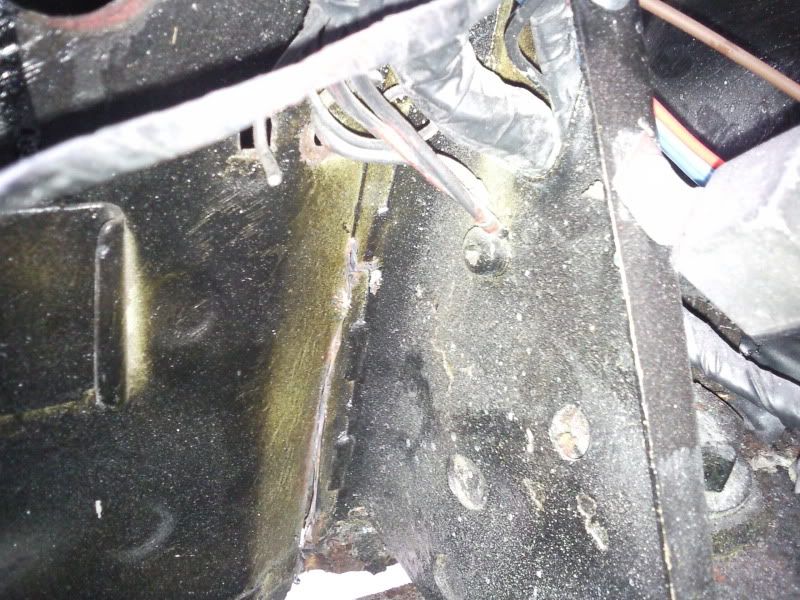
The cut i've made to the right of that was probably abit far over really, because the metal to the right of that is only the single skin of the inner wing, so not really suitable to weld the bottom plate onto.
So I tried splitting the inner wing skin from the strengthening plate behind, thinking that the bottom plate could be welded to that, but I can't really split them apart, and I can't even tell where the spot welds are.
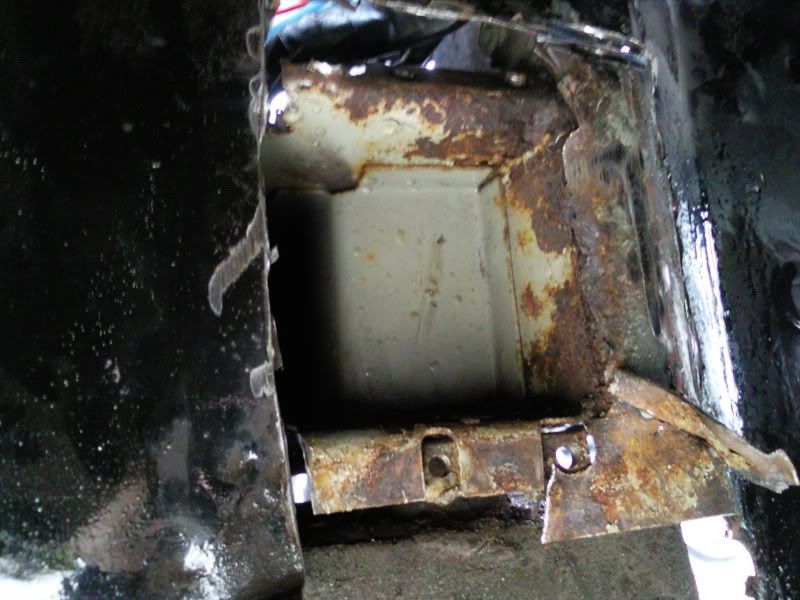
Also the bottom mounting block for the shock mount bolts doesn't really seem to be held into the box section, its connected to the inner skin either by rust or a spot weld. I'm starting to think that getting studs welded onto the repair plates maybe a better idea than those little boxes.
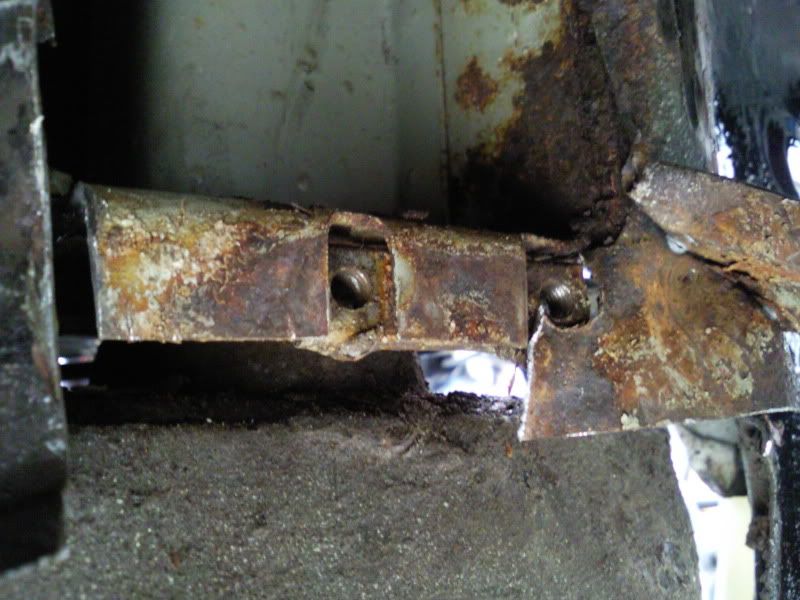
So yeah i'm not really sure what my next move should be. I don't know if I should try and cut the welds inside the inner wing to try and release the chunk of metal left - But I know I can't get my grinder in there and the wiring loom is right in the way aswell. Or if I should try and split the 2 skins apart and left the inner skin in place. All i'm thinking at the moment is where the welder is going to weld the bottom piece into if I just cut it all out
1 user(s) are reading this topic
0 members, 1 guests, 0 anonymous users