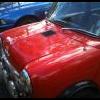
Boost Gauge And Pressure Calculations
#1
Posted 06 August 2010 - 07:58 PM
I'm anxious that the pressure will be too high and would like to be able to see exactly what it is. So, I'm considering fitting a boost gauge - a mechanical one.
It looks to be fairly straight forward - attaching a pipe with a brass fitting on either end. It looks as though the pipes you can buy are plastic, but if this connects into the inlet manifold under the charger, won't the plastic melt with the heat?
Also, can someone explain to me how to work out what the pressure is likely to be?
I have been reading up on it but just can't piece it together, and I certainly can't read the Eaton performance maps.
I'm charging a 998cc engine with 34cc upswept volume in the cylinder head CR = 8.4:1
Crank pulley 108mm (I think)
Charger pulley 65mm
Drive ratio = 1.66
therefore at 6,000 rpm engine speed, charger speed will be 6000 x 1.66 = 9970rpm
Something else about flow rates but here it where I get lost...
How do I get to psi from here???
Is there a simple method to gauge pressure from relative rpm??
#2
Posted 07 August 2010 - 08:22 AM
I'll try find the link..
Edit: it's at the bottom of this page;
http://www.eaton.com.../Superchargers/
Edited by Sammy D, 07 August 2010 - 08:24 AM.
#3
Posted 09 August 2010 - 02:56 PM
I looked up the pressure formula online so I'll post my numbers a bit later on. It came out around 7 psi though at 6,000 rpm (engine speed).
#4
Posted 09 August 2010 - 06:00 PM
#5
Posted 09 August 2010 - 06:51 PM
VMAX Crank Pulley Circumference = 108mm (I think)
Standard S/C Pulley Circumference = 65.5mm
108/65.5 = 1.65.
Therefore drive ratio = 1.65:1
@ 6000 engine rpm = S/C spinning at 6000 x 1.65 = 9900 rpm (optimum S/C speed is 10,000 above which S/C converts energy into heat rather than HP)
M45 supercharger output capacity = 45 cubic inches of air per revolution = 737cc's = 0.737 litres
So, 0.737 litres for 1 rev
therefore 0.737 litres x 9900rpm = 7296 litres per minute
Convert into cubic feet per minute = 7296 x 0.0353146667 = 258 CFM
998cc engine will displace 499cc’s per revolution (1/2 engine capacity)
therefore 0.499 litres x 6000rpm = 2994 litres per minute
Convert into cubic feet per minute = 2994 x 0.0353146667 = 106 CFM
or using a different calculation:
(cubic inches*RPM/3464) 60.9*6000/3464 = 106 CFM
Excess air = 258 – 106 = 152 “boosted” CFM @ 6000rpm
Boost = (excess CFM / normal CFM * atmospheric pressure) - constant for atmospheric pressure
(152 / 106 * 14.7) – 14.7 = 6.4 psi @ 6000 rpm
Does seem a bit low. Does this look right, or have I missed something? Perhaps I need to control for 85% Volumetric efficiency?
#6
Posted 09 August 2010 - 09:27 PM
I don't really follow your maths to be honest, but it is wrong somewhere.
At nearly 10k rpm you'll be pumping enough air for 150bhp. But you'll also create around 20+ psi of boost, which is so far off the published map http://www.eaton.com...t/ct_128483.gif that you'll probably melt your inlet manifold!
#7
Posted 09 August 2010 - 09:52 PM
My maths must be wrong. Can someone please shed some light.
#8
Posted 10 August 2010 - 07:28 PM
Furthermore, I research the old shorrock C75 supercharger for comparison and that also displaces 750cc's per revolution and with approximately a 1.08:1 crank to charger pulley ratio, it was generating 10 psi @ 7,000 rpm. With almost a 1:1 ratio the charger is spinning marginally faster than the crank. I know they are different types of supercharger but how can the figures come out so different?
Plugging the shorrock figures into my formula gives the psi mentioned above, so how come the eaton figures are way out?
Seriously confused...!
Shorrock C75b – 750cc per rev
(89/82) = 1.0854:1 pulley ratio
(1.0854 * 14.7 * 750 / (998/2) ) – 14.7
(15.96 * 1.503) – 14.7 = 9.3 psi
Eaton M45 – 750cc per rev
(110/65.5) = 1.680:1 pulley ratio
1.680 * 14.7 * 750/ (998/2) ) – 14.7
(24.687 * 1.503) – 14.7 = 22.4 psi
Whichever way I do it now I always get 22.4 psi.
I'm going to do a compression test on the inlet manifold when the charger is installed since I can't rely on my Maths! Makes we want to abandon the project so my engine doesn't blow up!!
Edited by Verbaliser, 10 August 2010 - 08:36 PM.
#9
Posted 13 August 2010 - 09:57 PM
the engine consumes 499cc per revolution the charger makes 737cc per revolution (@ 1:1) the difference is the pressure
737
___
499 = 1.48
1.48 x 14.7 - 14.7 = 7.01 psi gauge
or with a 1:1.66 ratio ((737x1.66/499)x14.7)= 36.04-14.7 = 21.34psi gauge
Edited by Brett, 13 August 2010 - 10:14 PM.
#10
Posted 13 August 2010 - 10:09 PM
if the supercharger can even run that high pressure the temp will be in the clouds soo on conclusion the 1.68 ratio on the charger will end in tears
cr 8.4, no intercooler, suck through fueling?, id rather not

Edited by Brett, 13 August 2010 - 10:18 PM.
#11
Posted 13 August 2010 - 10:16 PM
#12
Posted 13 August 2010 - 10:18 PM
#13
Posted 16 August 2010 - 09:26 PM
Because I am running a SWIFTUNE SW5-07 camshaft, I have to account for 25 degrees of valve overlap (calculations pinched from forum posting by AC Dodd Engineering, Nov 2009). The pressure calculation previously discussed, says that roughly there is 5% reduction in boost for every 10 degrees of overlap. Therefore, the psi figure will reduce by 5% x 2.5 = 12.5%.
Apparently different cams will have different valve overlap and is calculated by adding the first inlet figure and last exhaust figure.
E.g. For SW5-07 - Timing: 10/52 (inlet) 47/15 (exhaust). So overlap = 10+15 = 25 degrees.
So, I have amended my calculations;
Using stock 65mm cooper s pulley - 19psi at 10,076rpm (charger speed) 62% thermal efficiency
Using 83mm pulley - 12psi at 7,952rpm (charger speed) 65% thermal efficiency
Using 92mm pulley - 10psi at 7,174rpm (charger speed) 66% thermal efficiency
Maximum charger thermal efficiency is 67% based on my interpretation of the Eaton Performance Map. Basically, thermal efficiency is power you get out / power you put in. Therefore the higher the better.
So, using 92mm pulley (simplified somewhat):
(Pulley ratio x pressure ratio x 1 atmospheric pressure) - 1 atmospheric pressure
Pulley ratio =110mm (crank pulley) / 92mm (s/c pulley) = 1.2
x
Pressure ratio = displacement of M45 737cc / engine capacity 998cc divided by 2 = 737 / 499 = 1.48
x
1 atmospheric pressure, 14.7 psi
So,
(1.2 x 1.48 x 14.7 ) - 14.7 = 11.3psi
minus adjustment for boost lost from valve overlap
=11.3 - (11.3 x 12.5%) = 9.85
final figures based on full values (not rounded as above) and gives a hteoretical boost figure. Actual may be affected by other factors.
Now I have to decide if I want an 83mm or 92mm supercharger pulley - Jonspeedracing can make any size apparently for £60.
Thoughts anyone?
#14
Posted 22 August 2010 - 01:48 PM
#15
Posted 24 August 2010 - 08:33 PM
Just to make sure though I have purchased a 52mm Stack mechanical boost gauge which i'm going to plumb into the underside of the manifold with some silicone 3mm tubing. I might get an overbraid kit or heat shield tape for the pipe to protect it a bit more from the heat of the exhaust. Hoses good for 200 degrees - hope that's enough - don't want it to melt
Fingers crossed!
I hope I'm on the right lines....
1 user(s) are reading this topic
0 members, 1 guests, 0 anonymous users