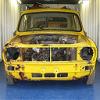
1979 Rust Heap Clubman Rebuild
#256
Posted 19 November 2012 - 02:11 PM
Darren
#257
Posted 19 November 2012 - 06:12 PM

#258
Posted 22 November 2012 - 12:46 PM
#259
Posted 25 November 2012 - 08:13 PM
So after reading what you guys said above, I decided to take your advice and get the floor inside the heelboard. I made a little cut at each corner and bent the lip down with some mole grips. With the floor inside, I returned the lip to its correct position with the help of a calibrated impact tool (size large, or course). Glad I did this, because it looks much more factory this way.

The floor is plug welded in at the heelboard end, and I also added some stitch welds to the bottom for extra security. Then came the weldathon to attach the new floor to the tunnel. I took a long time over this, allowing each 5cm of seam weld to cool before moving on to avoid warping. Didn't do too badly. There is a bit more more welding to do under the rear squab and then a lot of grinding and tidying up, but I was pleased to get this far with it today. :)

#260
Posted 25 November 2012 - 08:35 PM
#261
Posted 28 November 2012 - 11:20 PM
Pete
#262
Posted 29 November 2012 - 11:02 AM
(famous last words)
Keep it up.
#263
Posted 06 January 2013 - 09:08 PM
Crossbow:I wasn't sure before I started either, but if you take your time and read enough threads on this forum, its not too difficult to get started. :)
Onto side 2 of the floor! After doing the first side, this should have been a piece of cake, but it still took ages. This time, having learnt the heelboard lesson from last time, I cut and bent out the flaps right at the beginning. The crossmember needed a lot of rust repairs on the driver's side, so I did the necessary rebuilding and painted the inside with POR15. This is a bit of a milestone for the project as this floor panel is the last rusty panel to get the chop. With the exception of a few remaining small areas, there are no more rusty panels to replace on the main shell. :)

New floor/sill panel primed, rust protected and drilled ready for welding in.

Fitted in place with most of the plug welds complete, and tacks along the seam. Intergrips are a godsend when fitting floor panels!

The view from underneath...

As with the passenger side, I kept a chunk of my previous floor repair in place at the heelboard end because it was too integrated into the companion bin stuff to remove.

Post weld and grind:

This area still needs a bit of additional welding from the inside.

Finally! Both sides of the floor (mostly) complete! There is still some welding to do to join up some gaps on the inner sills and floors towards the back end, but I was able to remove the bracing as the shell is now strong enough to hold its own shape.

Next job after finishing off tidying up the floor welding is to paint strip and prime the tunnel and crossmember.

#264
Posted 06 January 2013 - 09:12 PM
I would consider now seam welding that end up so its water tight.
#265
Posted 06 January 2013 - 09:16 PM
Keep going.
Graham
Just beat me to it Neil !!!
Edited by grahama, 06 January 2013 - 09:16 PM.
#266
Posted 06 January 2013 - 09:18 PM
Great job there. Nice methodical work, you must be very pleased. I would tho add some weld to the end of the sills at the heelboard end to close any areas open to water and grind flush. Sorry if you have stopped prior to doing this but just a thought.
Keep going.
Graham
Just beat me to it Neil !!!
Got to be quick Graham and a happy new year to you as well mate.
#267
Posted 06 January 2013 - 09:18 PM
Oh yes - now that you mention it that makes perfect sense. I think my approach to that area has been completely ass-backwards because I didn't want to undo too much of the work I'd already done there. Oh well - I'll do as you sgeest and seam weld up the edge. It will look a lot neater like that anyway!
#268
Posted 06 January 2013 - 10:04 PM
#269
Posted 07 January 2013 - 07:44 AM
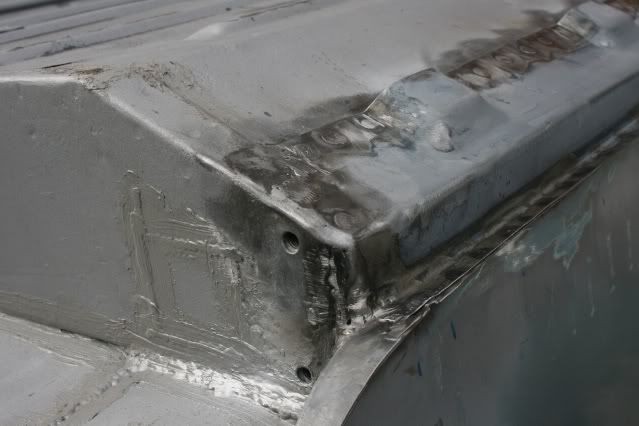
If you grind it back too much just pop a bit more weld in till it's all smoothe ish and closed up.
Graham
#270
Posted 07 January 2013 - 06:57 PM
1 user(s) are reading this topic
0 members, 1 guests, 0 anonymous users