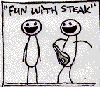
Flo's Body Resto
#46
Posted 24 March 2010 - 08:19 PM
You can get that sound deadening from any bodyshop suppliers, or even online.
#47
Posted 24 March 2010 - 08:23 PM
Top quality work
![]()
What do you use to dress down the welds?
Metal grinding stone on a grinder, followed by 60 grit fibre discs on a backing pad on the grinder, and a die grinder and a belt sander for tricky bits.
Any chance of some pictures of these Pete?, as i could do with getting something decent to finish welds.
Wish i could make panels like that!
It's just a normal 4.5 inch grinder with a metal grinding stone, the same grinder but with one of these with a 60 grit fibre disc, a die grinder with a conical metal burr, and a normal 520mm long belt sander.
Cheers Pete!

#48
Posted 24 March 2010 - 08:27 PM
Queue lots of pictures or rusty holes..
Rear floor area
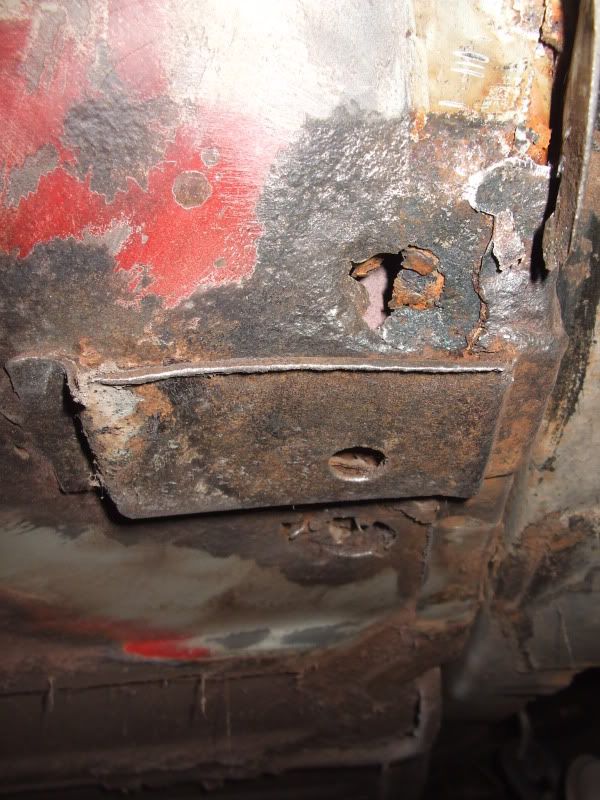
Middle of inner sill
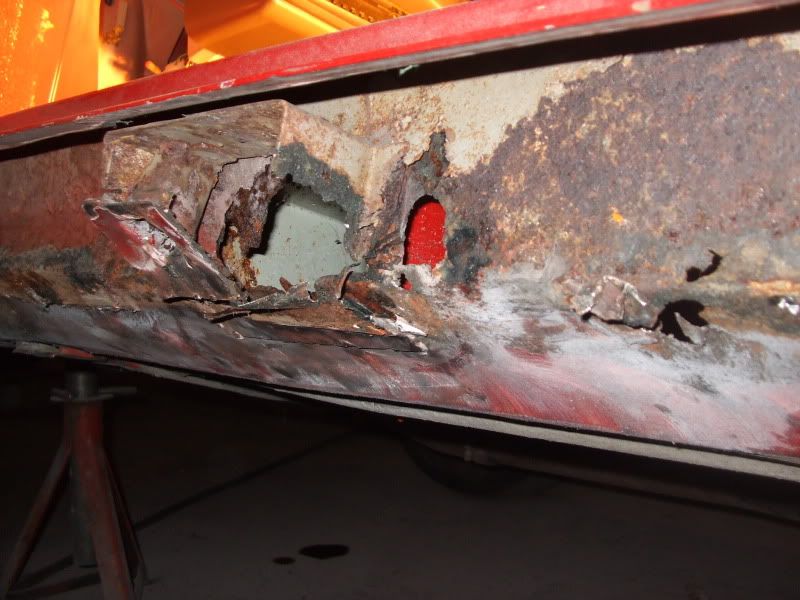
Front of inner sill
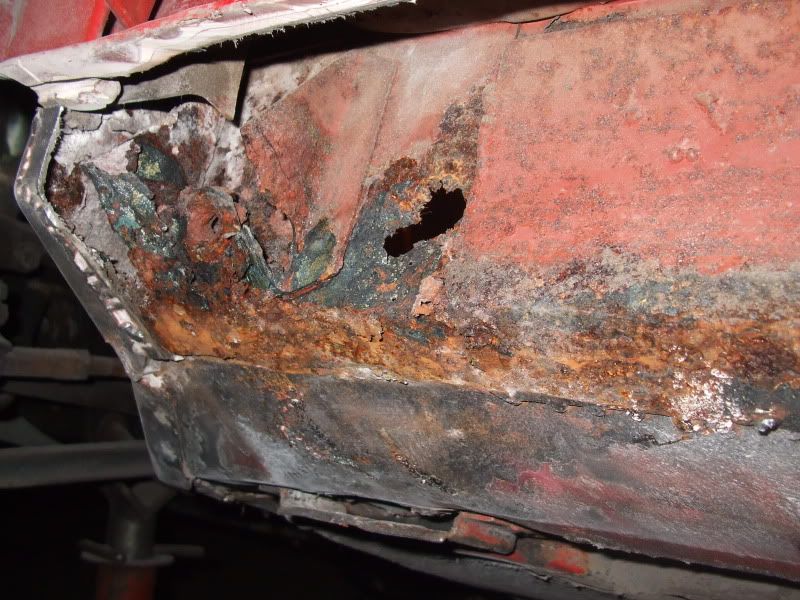
Rear subframe mounting point - no welding required!! yippeee
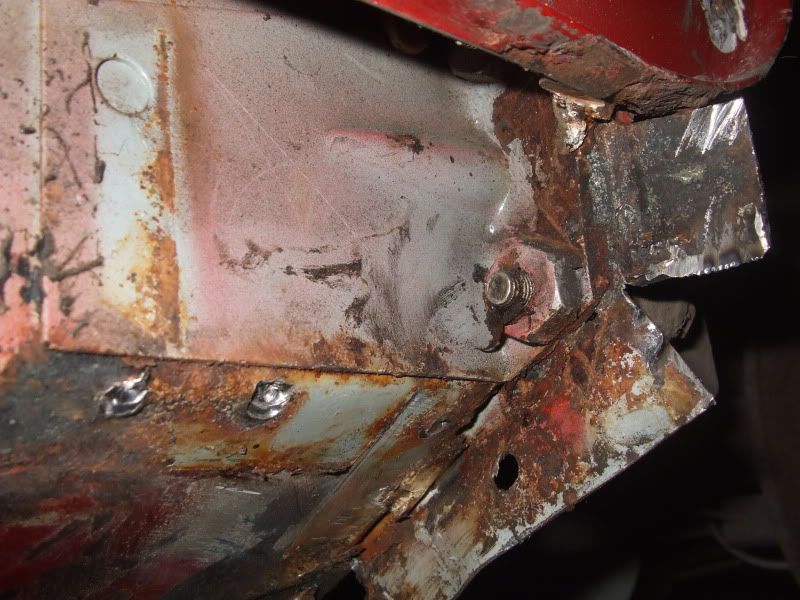
2 little holes in the front floorpan
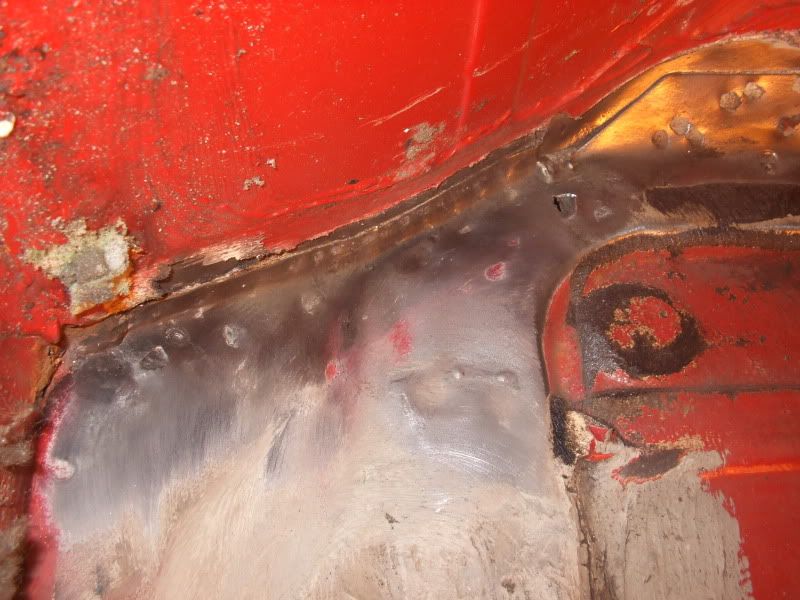
Another nice plate on the flitch, welded by me, before seam welding had been invented.
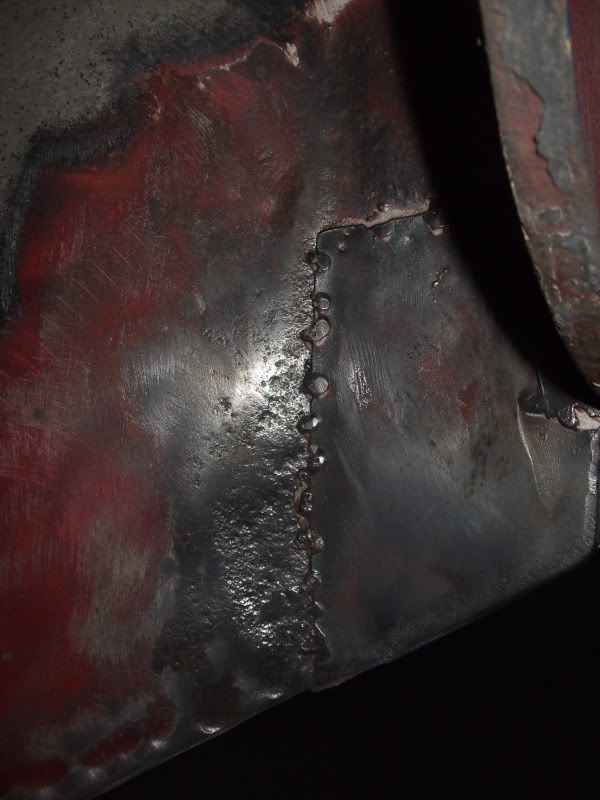
Hole on bottom of rear quarter
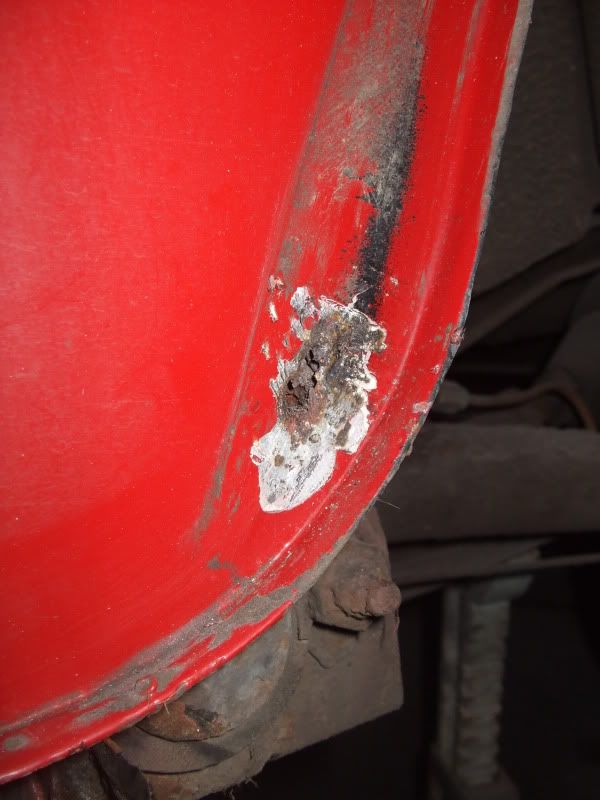
Holed rear bin area
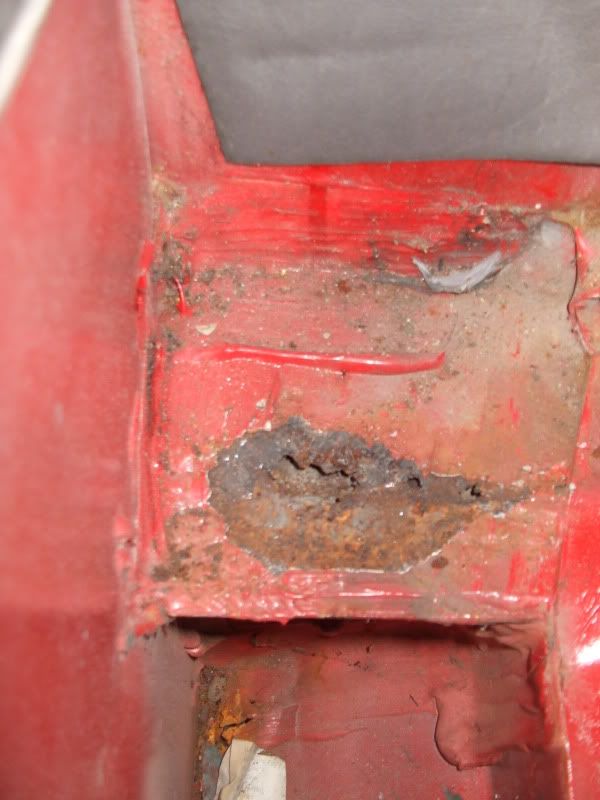
Got a little welding done tonight, cut out the rusted area of the rear floor
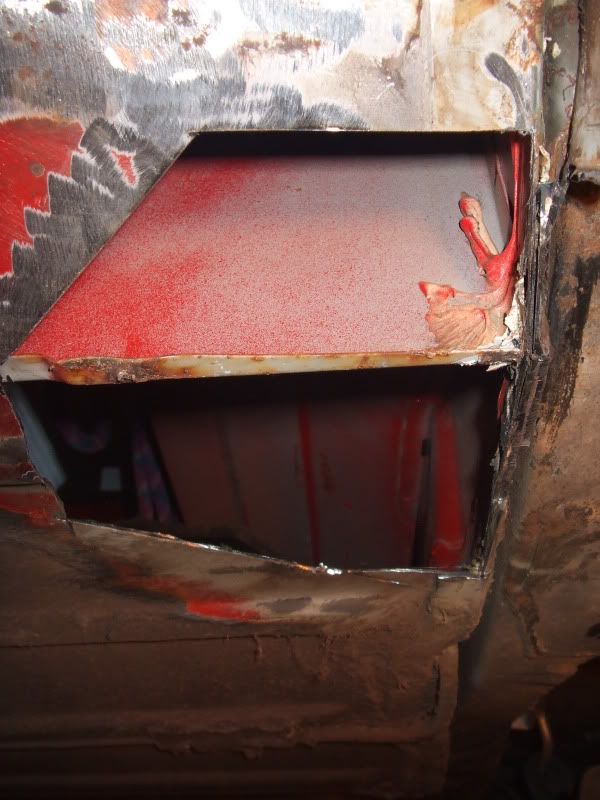
Plate made and tacked in
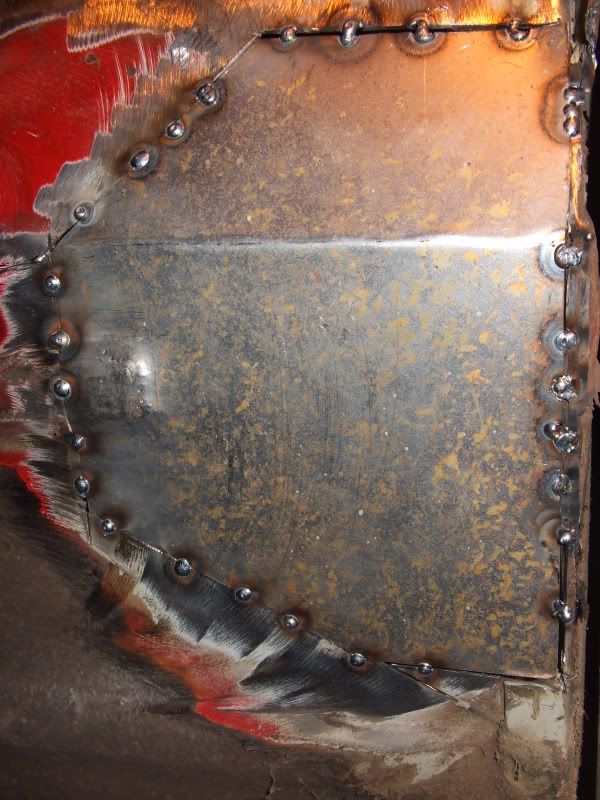
Plate fully welded with new hanger bracket
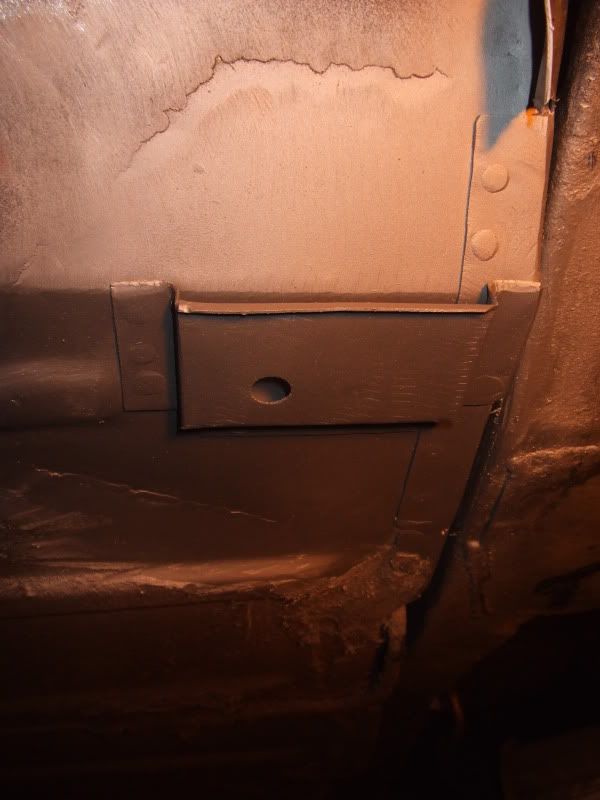
#49
Posted 24 March 2010 - 08:46 PM
other than that fancy a weekend in my garage it's taking me ages to get my outer cills off


#50
Posted 24 March 2010 - 09:11 PM

Cheers..
#51
Posted 24 March 2010 - 09:21 PM
#52
Posted 24 March 2010 - 09:53 PM

#53
Posted 24 March 2010 - 10:25 PM

Pauly - I just marked where the bump should go on the plate, and hammered it over an open vice, open to the same width of the bump, with a panel hammer.
#54
Posted 24 March 2010 - 11:09 PM
But seriously, it will be another minter when you've had your wicked way with it.
Is it staying COF?
#55
Posted 25 March 2010 - 08:44 AM

And yeah it's staying flame red, it's the colour it left the factory in, and I don't want to have to repaint the inside

#56
Posted 25 March 2010 - 02:06 PM
Just purchased one of those backing pads and some 60 grit fiber discs. Cheers PeteIt's just a normal 4.5 inch grinder with a metal grinding stone, the same grinder but with one of these with a 60 grit fibre disc, a die grinder with a conical metal burr, and a normal 520mm long belt sander.

#57
Posted 25 March 2010 - 05:13 PM
#58
Posted 25 March 2010 - 07:45 PM
I shall be warey!Cool! just don't dress it too much, or you can end up burning through!

#59
Posted 27 March 2010 - 04:14 PM
Attack it with vengeance!

i hope we'll be seeing you al malvern!

keep the good work up! x
#60
Posted 27 March 2010 - 05:15 PM
Ta ta
1 user(s) are reading this topic
0 members, 1 guests, 0 anonymous users