
'busavan
#61
Posted 23 November 2011 - 09:45 PM
#62
Posted 23 November 2011 - 09:49 PM
#63
Posted 24 November 2011 - 04:30 PM


There is a small update to the thread that i am working on, nothing much, just the way i have done the coolant pipes and other pipework

Edited by rustandoil, 24 November 2011 - 04:31 PM.
#64
Posted 24 November 2011 - 08:05 PM
#65
Posted 04 December 2011 - 08:32 AM

After a lot of careful measuring and cutting i am very pleased with the result

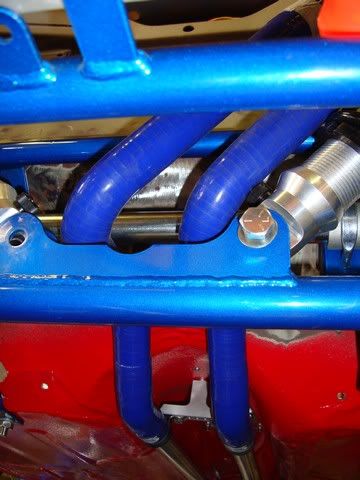
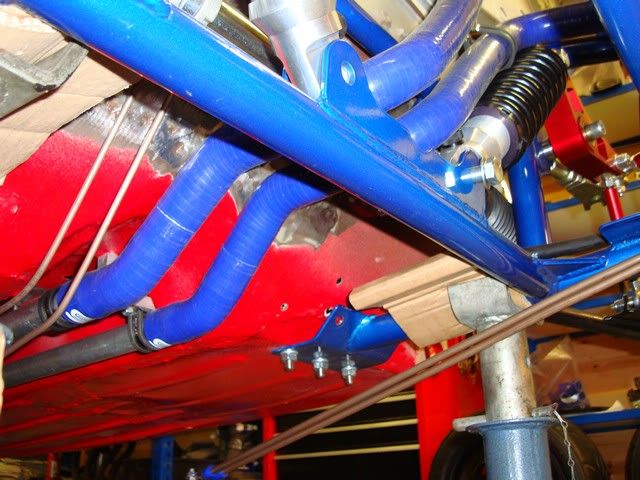
I mounted the servo so i could get the brake pipes sorted out, also the clutch reservoir on a alloy bracket, i have chosen to use copper nickel from front to rear, probably not my best decision as i don't really find it too easy to work with and has caused a few headaches

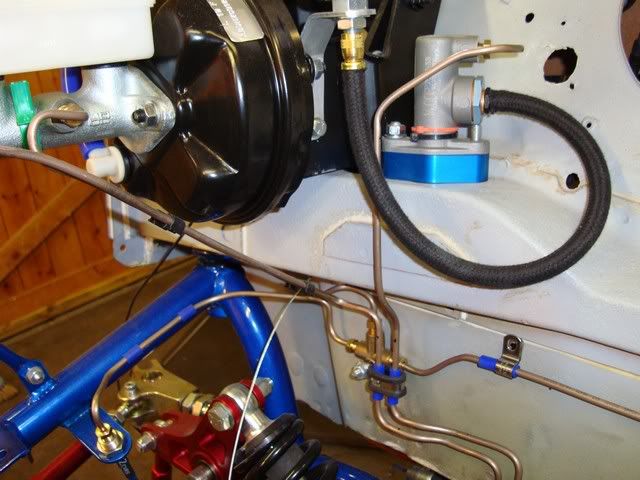
Because of the decision to use copper nickel pipes i found it was going to be very difficult to get them in the tunnel particularly where they have to exit around the frame at the rear, so i have decided to run them along the underside of the floor, not what i really wanted but if secured with some nice clamps i am sure they will be fine.
I have designed the pipe clamps and had my toolmaker (thanks Bri) make up one to see how its going to work, seems ok just need a gap in the paid w


All well and good but i am worried that i may have a clash of mounting points with my seat mounting so i have now ordered seats which will be fixed in place the i can see where i can fix the pipes.
The rigid pipes terminate at the rear on this alloy bracket with braided hose to each rear brake and the clutch, the fuel pipes which will also be copper nickel front to rear will also terminate to flexible at this bracket, i will post more pictures as this idea develops.
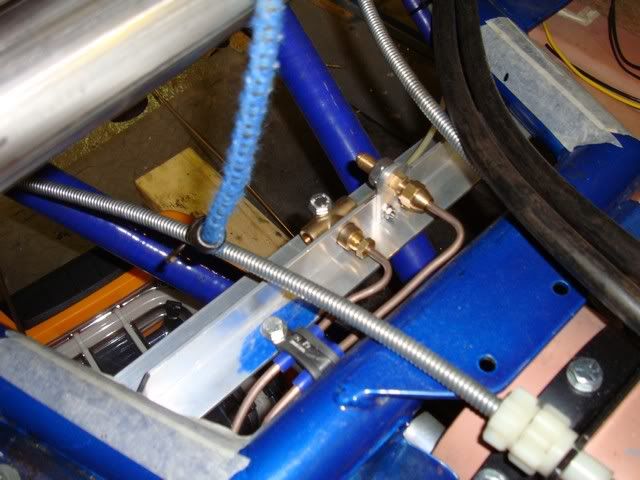
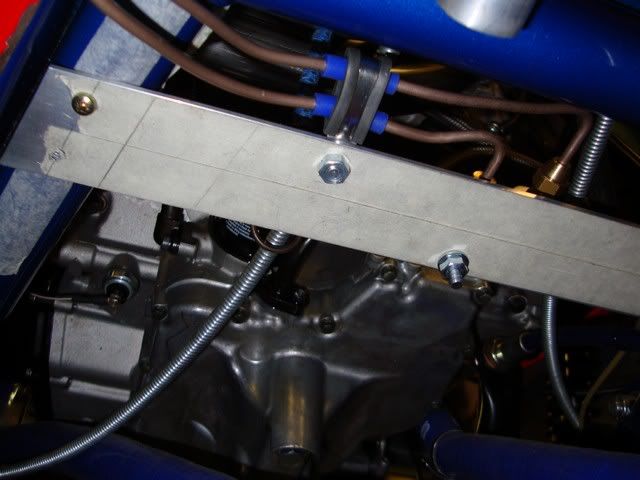
If you have read the beginning of the thread you might remember that i bought the van as a unfinished project it came with both fibreglass and the original steel doors, the fibreglass doors do seem to fit quite well, but i don't have a clue about how to open up the frame to accept the window seal / runner nor any idea how to bond in something to support the bottom of the windows, so i decided to have a look at the steel doors, the drivers door seems to be in reasonable condition and a check with the spring balance suggests that there would not be a massive weight saving using the fibreglass doors especially after the removal of the steel door pocket, anyway the drivers door fits very will the passenger not so good but has a rotted out section and flexes about quite badly, i have read good things about the mini door company i will have a chat to them about repair and re-skin in alloy
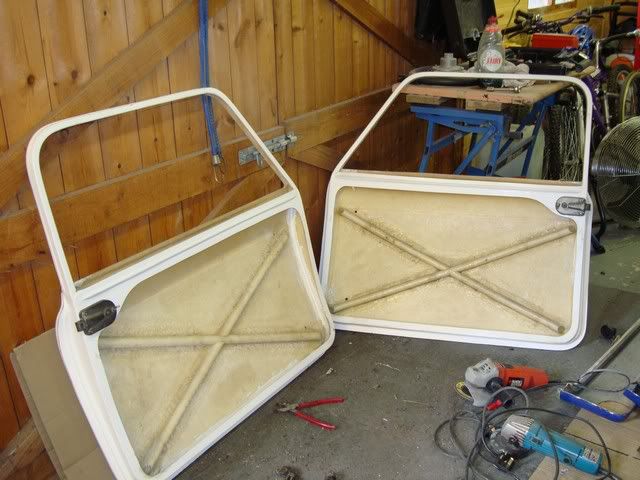
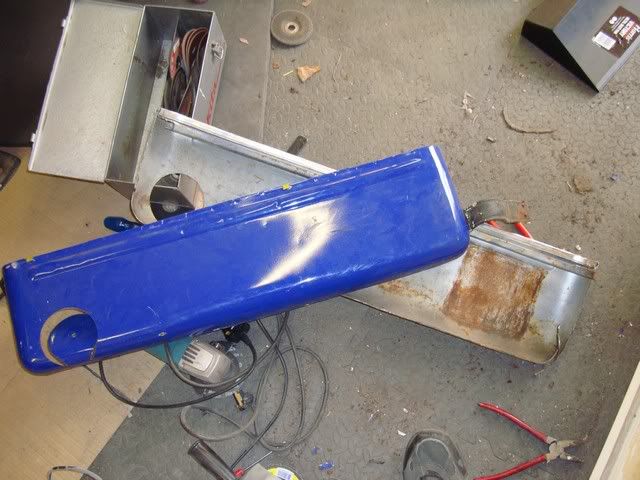
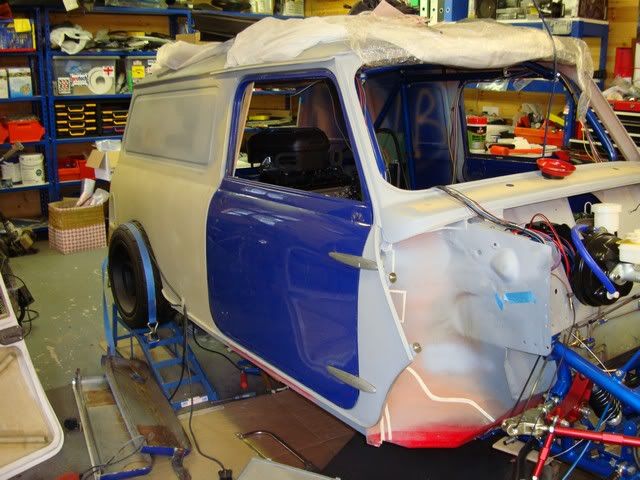
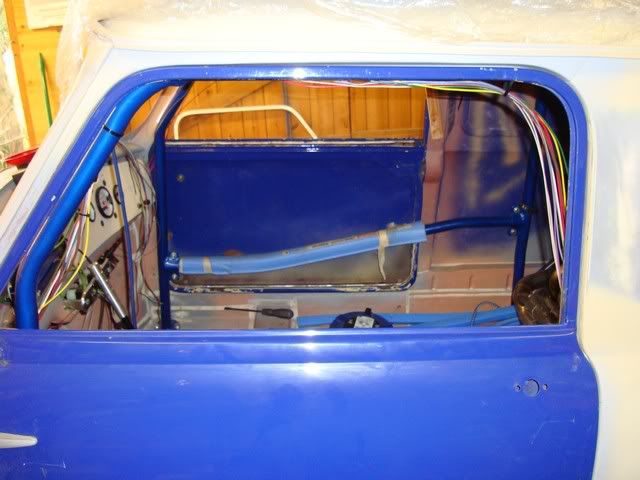
That's it for now, and indeed brings things pretty much up to date

#66
Posted 17 December 2011 - 06:17 PM
Would you consider making parts for others?
Al
#67
Posted 17 December 2011 - 08:10 PM
I mounted the radiator to see what needed to be done to connect the coolant pipes, i couldn't figure how the stuff i got from Z-Cars was supposed to work
so my fix was a trip to Silicon hoses (luckily only half an hour away) to purchase four 45 degree bends and some alloy joiners.
After a lot of careful measuring and cutting i am very pleased with the resultwont be quite so tidy when its got hose clips on
![]()
These may help, they get tighter with heat, think there called gates, saw them the other year on a mini at Bingley
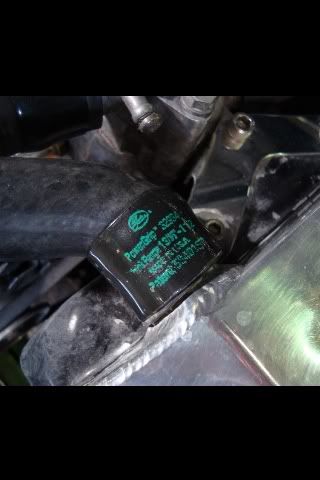
Great project, fantastic engineering work displayed
Andy
#68
Posted 18 December 2011 - 08:38 AM


Al, no promises as we as still new to the CNC game but PM me a drawing or sketch and we will have a look
Andy, as an engineer i like "mechanical fixings" but those Gates hose clamps would really neaten things up, i will try to beg some samples and see what they are like

link to the Gates hose clip catalogue page
Martin
#69
Posted 18 December 2011 - 09:03 AM

Loving the attention to detail and the fabrication facilities to get the job done right
Looking forward to more updates
Regards
Steve
#70
Posted 20 December 2011 - 08:16 AM
Clearly I don't need seats for ages yet, but in order to ensure the mounting points would not clash with brake, clutch and fuel pipes and their fixings i ordered these Corbeau Sprints with a bit of custom embroidery

Ordered on a Friday afternoon and delivered the following Thursday
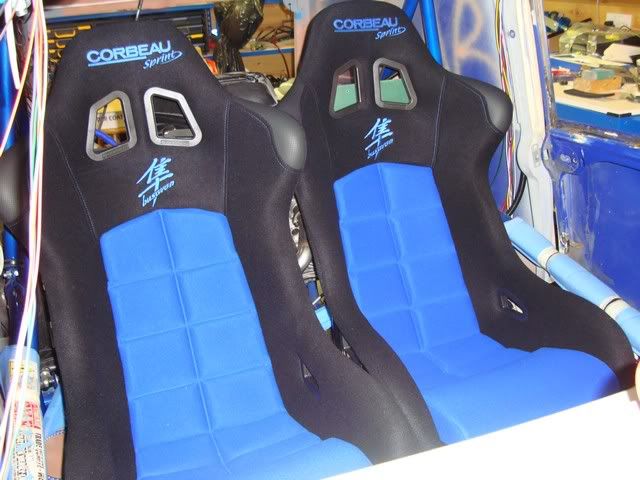
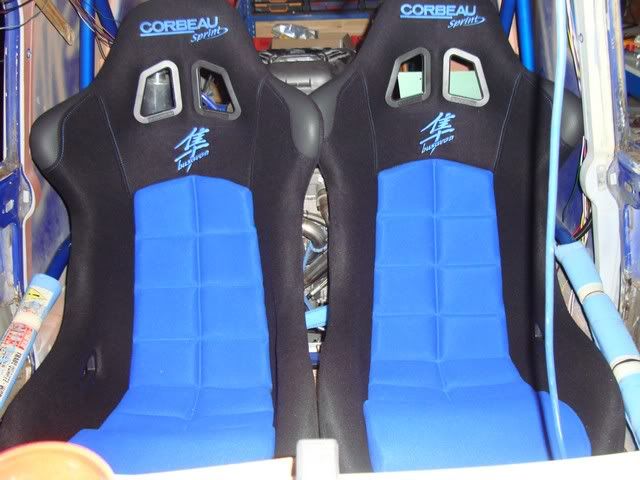
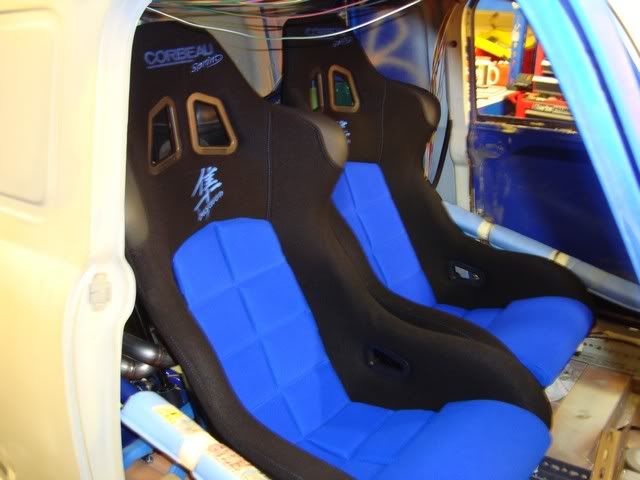
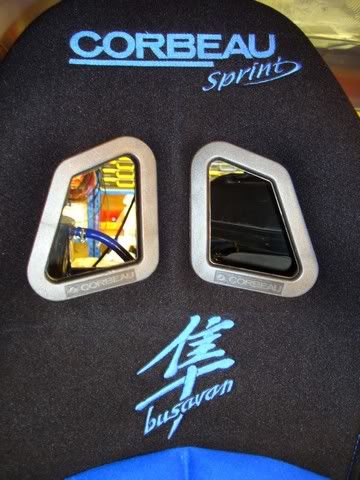
I was told by the very helpful Kathryn at Corbeau that the sprint would fit in a classic Mini but "would be tight" she was not kidding

We have started to make a new inner side mount for the seats from aluminium section we have also cut and machined some aluminium angle and "T" section for the basis of the seat subframes, very much a "make it up as you go along" job......
There will of course be photos of these parts when we are a fit further on........
#71
Posted 20 December 2011 - 08:28 AM
#72
Posted 20 December 2011 - 10:20 AM
#73
Posted 20 December 2011 - 10:13 PM
All the custom made parts are lovely.
#74
Posted 21 January 2012 - 04:45 PM
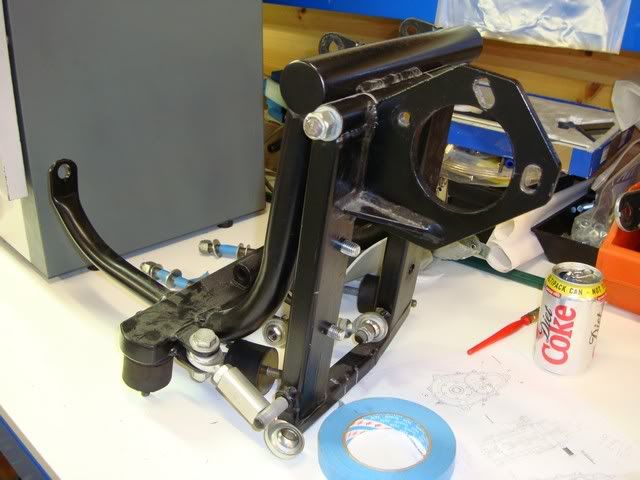
When refitted with the lower mounts the chain adjuster mount would have fouled the frame so i cut them off
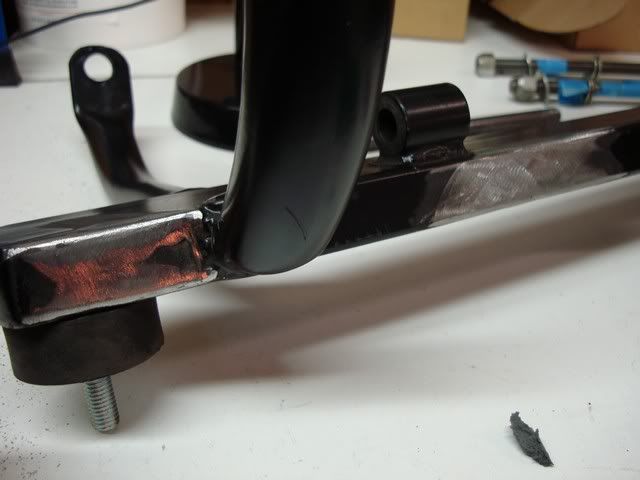
Checking the parts i have discovered more misery



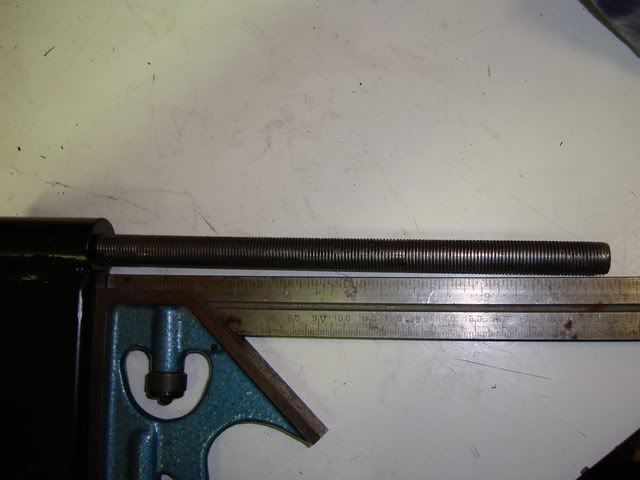
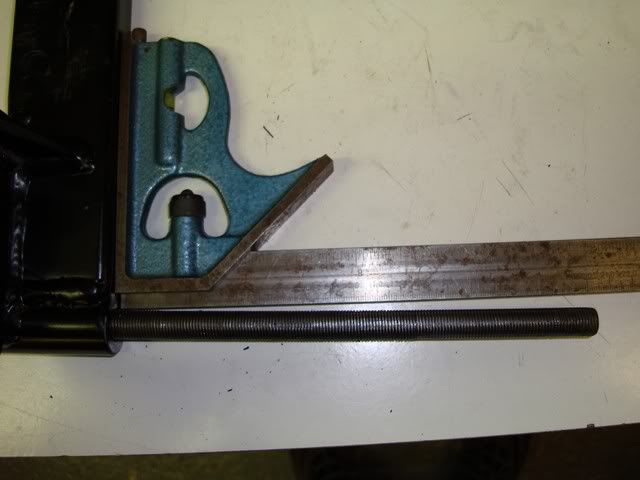
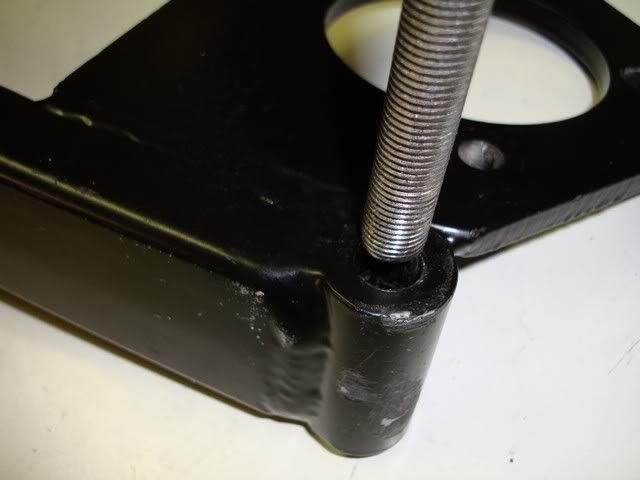
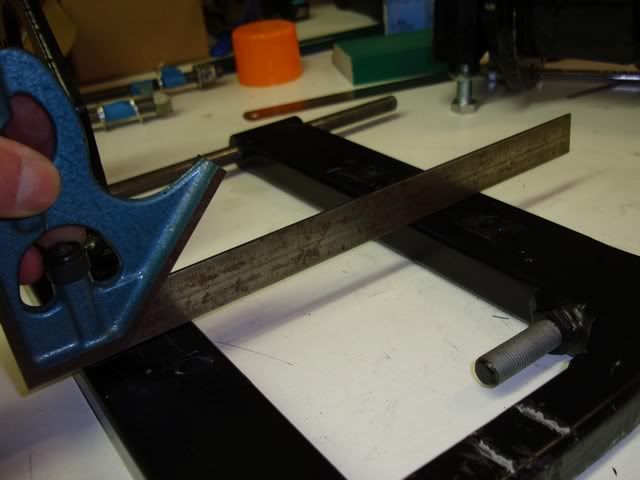
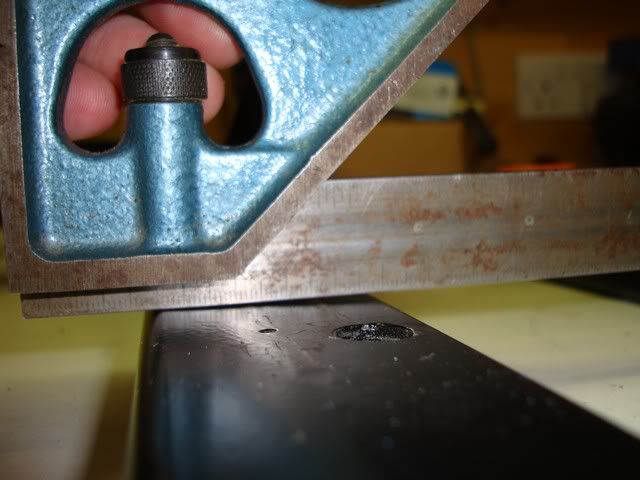
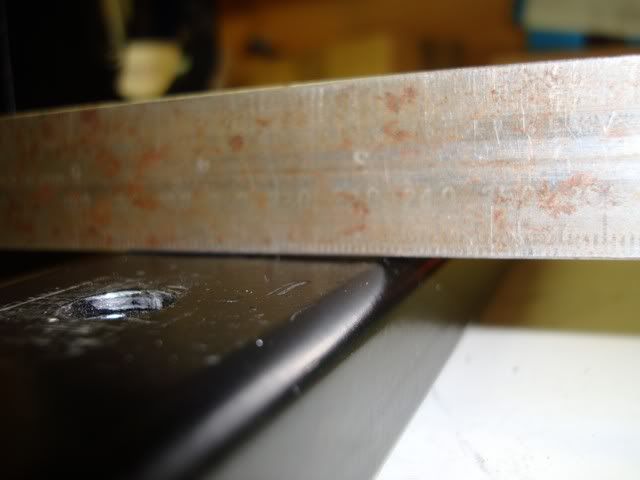
With the diff bolted to the mount it pulls everything around enough that it would (might) work but the top screwed rod needs quite a tap with a mallet to get it through the mounting bushes

Oh and the reverse ring gear supplied is too big

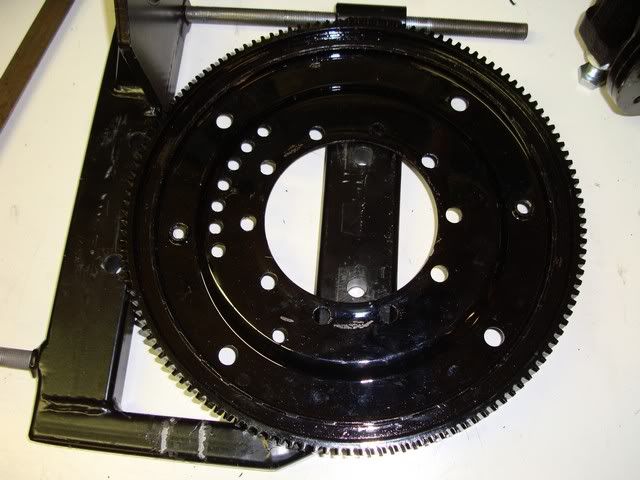
#75
Posted 21 January 2012 - 10:44 PM

i was looking at the photo of the exhaust manifold and noticed that you have got one of the oil pipes between the exhaust and the engine block. i would highly recommend either re routing the pipe away from that area or getting some heavy duty heat insulation wrap to cover the braided hose. when i had my mini out for a blast at night after returning home you could open the bootlid and clearly see the exhaust manifold glowing orange.

leave at least 2" between the aluminium bulkhead and the exhaust to allow air circulation, although your design of frame where the exhaust would have originally been will allow some air to get in and around the exhaust.
leave some space between the bulkhead and your seat otherwise the heat might damage your cracking seats.
Keep the pics coming, all this info helps the fellow builders

Ed
1 user(s) are reading this topic
0 members, 1 guests, 0 anonymous users