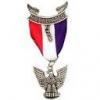
Anyone Have A Diy For Building Your Own Wiring Loom?
#1
Posted 24 July 2009 - 01:37 PM
Any tips or locations would be appreciated!
#2
Posted 24 July 2009 - 02:14 PM
#3
Posted 24 July 2009 - 03:57 PM
Like marriage, "not to be undertaken lightly......".
#4
Posted 24 July 2009 - 05:25 PM
If you do it properly, it won't work out much cheaper than buying a ready made loom, and it will take you a long time to do it, but its worth it if you want a more reliable fusebox that can be mounted wherever you like, plus lots of extra stuff can be wired in as well.
Sy
#5
Posted 24 July 2009 - 06:39 PM
#6
Posted 24 July 2009 - 06:46 PM
If you really want to build your own harness get a good book on auto electrics, it really is NOT as simple as some people will have you believe
Ok if you are still going to build your own harness, then remember the FUSE is there to protect the wires..... and ultimately you the driver and your passengers

PS Autosparks prices do not include VAT.......
#7
Posted 24 July 2009 - 08:09 PM
#8
Posted 24 July 2009 - 08:42 PM
Did this years ago for a Rally Mini - lot of relays and fuses - first make a drawing of what you need - then get ON with it . It's EASY! Just use red wire throughout - with numbers on the wires. Simples !
Using oen wire throughout must make fault finding later on rather hard?! Even if they are numbered?
#9
Posted 24 July 2009 - 09:32 PM
#10
Posted 24 July 2009 - 09:54 PM
I ordered 30 different coloured 4 meter lengths from autosparks (30 was tight, I had to re-use some colour on some of the shorter lengths around the dash etc, but kept the duplicate colours to circuits that are far apart to prevent confusion) - the thinwall stuff, a couple of blade fuse holders, some heavier guage wiring for higher power things like the lighting circuits, a battery isolator switch, several meters of spiral conduit and even with shipping from uk to france, it was all under £50.
I spent a few evenings copying the circuits from the haynes into a new design. I laid it out on paper as it would be laid out in the car (the haynes diagrams are laid out for ease of drawing and bear little resemblance to the cars physical layout).I then started in the car, laying each wire one at a time and marking what colour I used on the diagram. I left each wire a good bit longer than needed at both ends, so they could be neatly cut down to the correct lengths once wrapped.
looks like a nightmare, but with the plan i had drawn (a2 sized bit of paper), it was all easilly traceable....

Once spiral-wrapped it looked more civilised!

The majority of the loom follows different routings to the standard one to keep it hidden, and to keep the fuseboxes inside the car. Decent grommits were used wherever anything asses through a panel, and the spiral wrap keeps it neat, allows additional wiring to be added later, should I want to, and looks very neat, without the hassle of wrapping with loom-tape. (DO NOT wrap the whole thing with insulation tape, it makes a hellish sticky mess should you need to undo a section later) I also added relays for the lighting circuits, and the hazard flasher is moved inside the cabin too. The engine bay is almost completely wire-free...

I kept the standard switchgear, and soldered the new wires to the original connectors, or used waterproof heatshrink crimps where this was not possible.
I now have a loom that is easilly traceable should I need to fault-find anything. Pretty much every electrical item is on a seperate circuit with a dedicated fuse and a dedicated earth point where required. The fusebox is inside away from dirt and damp, and relays mean that the current loading on the lighting switchgear is greatly reduced. I also have the main isolatoer switch which is within easy reach when sitting in the car and kills all circuits completely, should the need ever arise.
#11
Posted 24 July 2009 - 09:57 PM
#12
Posted 24 July 2009 - 10:14 PM
#13
Posted 25 July 2009 - 12:01 AM
For instance a rule of thumb is that for 1mm square (area) of copper wire you can allow 10Amps of current flow..... now if you then perform all the correct calculations based on each wire you then need to apply a "bundle" factor as most harnesses will consist of upwards of say 10 circuits.... this factor WILL reduce the amount of current permitted per circuit lets give it an arbitrary figure of 8Amps this by the way is due to induction within the wires, now this particular wire bundle happens to pass via a heater pipe which will raise the temperature and could quite easily raise it to a higher figure than the insulation is capable of carrying, so the wire melts the insulation and cuts through it like a hot knife through butter, only butter doesn't then go thermal by contacting other butter like the copper strands do as they coinnect with another wire... lets just assume that this second wire is a 27Amp main light switch power cable so this will allow current at 27amps to flow in to the reduced 10amps circuit thus creating a super heated butter knife..... this is what happens and it can happen to harnesses that have been designed and manufactured by Engineers that are specialised in this subject.
So if you still want to build your own harness find out what the current draw for each component is and add a safety factor.... buy 125 degree wire not standard 85 degree, do not solder joints on harnesses as this leads to fatigue (due to solder wicking up the strands) use proper crimp tools, Mac used to do a pretty good one for about £20
Never never never use house hold wire as it simply is NOT flexible enough and like soldering WILL fatigue

but most of all......... Do not forget to calculate your wire size based on current requirement, and heat and never go down in wire size just because that's all you have left

#14
Posted 25 July 2009 - 07:18 AM
Whilst what you say is correct, lets not get too worried about it - remember that a very large number of standard mini looms are in a shocking state....


and whilst many dont look as bad as that externally, 20 years of use, vibrations and infiltration of damp will not have done even the cleanest of looms any good.
As long as the wire used is over-specified for the circuits used, then there is no problem. The wire I have used on each circuit is at least 50% higher rated than required. Given that the maximum cable run I have is around 2.5 meters, the voltage drop is unlikely to be significant, or even measurable. Also, its all fused and the fuses on each circuit are rated at significantly lower ratings than the wire is capable of carrying.
The connections that I have soldered are not subject to any real stress or vibrations, with all other connections crimped with heatshrink crimps.
#15
Posted 25 July 2009 - 11:54 AM
It wasn't meant as a dig...... however your last post sums it all up really

Voltdrop can occur due to overloading a circuit, as you stated normal voltage drop along a cable should be minimal and yes it can be measured quite easily with a reasonable multimeter..... however if you start to overload a circuit then the internal resistance will cause a massive voltdrop / current increase cycle that ultimately will end in a thermal event

Over specify your circuits, include fuses etc just be careful, guessing can quite easily lead to issues later.
If you choose to put your lighting circuits on a fuse DON'T !!! put each headlamp and mainbeam on separate fuses, if one blows you still have some lights...... enough to stop safely

A simple approach is to measure the strands diameter in the circuits of you old harness and count the number, which would normally be in odd numbers 7/.028" for instance this will enable a cross sectional area to be calculated and some base figures to be determined.... remember a basic rule of thumb is 1mm2 is approximately 10amps.
By the way for military and aerospace its between 2.5 and 4amps per mm2
Use the higher grades especially in the engine bay..... the copper is good for upto 1500 degrees it's the insulation you have to worry about

Regards Martin
1 user(s) are reading this topic
0 members, 1 guests, 0 anonymous users