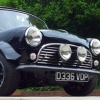
Stripped Centre Main Thread!
#31
Posted 15 June 2009 - 08:40 PM
#32
Posted 15 June 2009 - 11:36 PM
I wont say much about where you bought these parts. It pains me to see things like this happen, it is such a simple thing to get right, yet some of those who promote to be proffesional, turn out to be the ye ha's we should all avoid. However, despite the length issue, the bolts are the wrong High Tensile grade. Standard factory mains bolts are grade 8, the ones supplied in the strap kits are a lesser grade 5, excluding kits from Rob Walker, and now Minispares, (thanks to Turbo Minis) Why any of these other companies sell the kits with the lesser grade bolts, is one of the mysteries of the universe.
I have sent an Email to the person you bought the high tensile bolts from to ask the true length of them.
#33
Posted 15 June 2009 - 11:48 PM
#34
Posted 16 June 2009 - 12:46 AM
Even so, as a very basic guide that means you'd want 3 or 5 times the bolt diameter in thread engagement depth for there to be any chance of the block holding the bolt at its limit.
It seems elasticity is also important to resist fatigue. That's why big end bolts and good head studs are thinner in section on the, unthreaded, shank. It could be another reason why a stronger, higher grade, bolt isn't always better.
Boltscience.com - yes it really exists!
#35
Posted 16 June 2009 - 07:30 AM
When stretch is mentioned about bolts, its not about its elasticity.
The main point is, why use a lesser grade bolt in a critical aplication where a higher grade bolt was originaly used in the first place.
There is a very long topic about these very bolts on Turbo Minis, and there is some very good advice given by those who run some of the highest powered A series engines in the world. Advice worth noting, Don Not Use Grade 5 bolts.
#36
Posted 16 June 2009 - 08:15 AM
I would guess that some self "called engineer" (anyone who touches a spanner is now called an engineer) has been told about the "rule of thumb" and without thinking why its called a rule of thumb applied it to this application, hence why short bolts supplied with the kit. (please note we manufacture our own in higher grade steel to reduce material creep.)
Bolt grades are as follows .........
grade 5 = 500 N/mm2 (mm2 is the section area)
grade 8 = 800 N/mm2
grade 10 = 1000 N/mm2
grade 12 = 1200 N/mm2
This is a basic list and is only the tensile load nominal figures, but does give you an idea of how limited a grade 5 bolt is

Regards Martin
#37
Posted 16 June 2009 - 08:35 AM
Elasticity is important in ensuring the bolt doesn't deform plastically - as in yeild but also in resisting cyclic loading fatigue - of the bolt or the threads in the casting. There's also the possibility that a less stretchy bolt will overload the threads through thermal expansion.
I'm not saying higher grade bolts are automatically a bad idea (but it would be better if the thread engagement and torque was optomised for them) and practical experience is better than any amount of theorising.
#38
Posted 16 June 2009 - 09:03 AM
Elasticity is important in ensuring the bolt doesn't deform plastically - as in yeild but also in resisting cyclic loading fatigue - of the bolt or the threads in the casting. There's also the possibility that a less stretchy bolt will overload the threads through thermal expansion.
Thats the point, the bolts will not be exposed to cyclic loading as long as the pre tension, generated by stretching the bolt to 75% of its yield, by what ever means you use to tighten the bolt, be it turning torque, torque angle, or overall bolt length. If the force applied in the fixture is greater than the 75% of the yield of the fasteners, cyclic loading will eventualy cause the fasteners to fail with fatigue. So if the load is greater than 75% of the yield of the fasteners, you need to use a higher grade.
Anything exposed to cyclic loading will eventualy fail, you need to design out, where possable cyclic loading. Or, put in place methods that will not allow the fasteners to be in service longer than their fatigue life.
On another note, torque settings listed in the workshop manuals are for dry threads, lubricating the threads will see a higher pre load, and put the bolt closer to yield. Always apply oil under the head of the bolt as that is where much of the friction is in the fastener, next to the thread engagement. There is clearly some large leaway in those torque figures, as manufacturers have to consider the possabilities from dry thread to lubricated thread and be sure the bolt will not yield or be exposed to cyclic loading in service. Which is why a lesser grade bolt with lubricated threads using the standard torque setting is a bad idea.
PS. I am no Engineer, I am a technician

#39
Posted 16 June 2009 - 09:33 AM
Always apply oil under the head of the bolt as that is where much of the friction is in the fastener, next to the thread engagement.
PS. I am no Engineer, I am a technician
I wasn't having a dig at any one here... I was simply re-stating that which someone said earlier..... if you are going to design a product to sell, then you need to make sure ALL bases are covered.... I guess this is a simple mistake on someones part, but look at how much damage to other peoples property it has or could have caused

If the torque setting says dry then that is what it is tested at, oil under the head will also increase the preload, so will the material and the method used to create the bolt, and the type of finish ie zinc plate, chrome plate or simply self colour (bare metal)
as will the type of oil, the amount of oil............. even the simple fact that you may be reusing parts and the surfaces between the under head and the part the bolt head sits on could be work hardened and offer a lower friction......
However we are looking for consistency between ALL six bolts (in this case) ............. 75% is a chosen figure, due to a couple of limitations....... too low and the elastic region of the bolt will not be met and the fixing could easily work loose, too high and it enters into the plastic region, and once in the plastic region it can easily reduce down below the 75% point and ..... work loose.
Points to note...
Torque wrenchs are (sometimes) calibrated and always delicate.
Torque wrenches should NEVER be used to undo a fixing, as it will damage the internals... buy a breaker bar.
Torque wrenches are NOT hammers ... yes I have seen them being used for hitting things....

Torque wrenches are NOT levers
You should always leave a torque wrench at it's minimum position do NOT leave it set..... you wouldn't leave your car engine running 24*365 would you ?
Keep it in a clean dry environment, dust, dirt and water if allowed to get in WILL damage your torque wrench.
Have it recalibrated every 12 monthes, its relatively cheap, but will help to ensure that you get good results

I strive to keep Minis on the road

Regards Martin
#40
Posted 16 June 2009 - 12:20 PM
Or am I best to just use no oil on them during the build and use thecstandard torque settings?
#41
Posted 16 June 2009 - 01:46 PM
The main problem we are concerend with here is the grade of bolts used, no less than grade 8 should be used, which, for identification purposes is Imperial grade S or 6 dash marking on the heads. Three dash marking on the heads is a grade 5 bolt.
One way to check what the thread engagement should be is to take a standard bolt, place it in its hole in the bearing cap, and measure how much protrudes. That value will have been calculated by the engine deisgners, to limit the chance of failure in service. Look at it this way, the A series engine has been around for over 50 years, and there are millions of these engines out there that have no issue with the standard bolts. When modifying the engine, by fitting a strap on the center bearing cap, it would be wise to use a bolt that is either of equal quality or better, and has the exact same engaged thread legth. More thread engagement is not a problem if the holes are deep enough to take the extra. The biggest problem in the UK is the limitted stocks of good quality high grade Imperial dimention bolts, available individualy.
#42
Posted 16 June 2009 - 02:03 PM
Look at it this way, the A series engine has been around for over 50 years, and there are millions of these engines out there that have no issue with the standard bolts.
Just how many Minis do think there are in the world ? sorry off topic just interested thats all

#43
Posted 16 June 2009 - 02:38 PM
Thinks: Would it be worth modifying the non-'S' block to take fitted studs made from the right quality steel? Martin, is that something you could offer? I would be interested if you could. Two different lengths, One for standard caps and one for caps with the strap.
#44
Posted 16 June 2009 - 06:35 PM
That centre strap looks pretty thick to me, or is it my imagination? They are usually 7/8 or 1" thick.
I have another solution for you - one that might actually avoid the need for helicoiling. I'm going to send you some 'oversize' length bolts and a half-dozen extra high-tensile washers.
What this will hopefully allow you to do is drill out the damaged first 4-5 threads, then wind a tap down to make sure what's left is clean. This will hopefully leave you with sufficient thread engagement in the remaining threads to make this work.
What you'll need to do is take the longer bolts, wind them all the way in until they bottom out. Now, you'll slide the cap and strap next to the bolt(s) and then stack washers one at a time onto the top of the strap, until the cap/strap/washer height is greater than the height from the block face to the underside of the bolt head by 2 to 3mm (40-120 thou).
Now you can be sure that you have the absolute maximum thread engagement, that the fastener won't bottom out, and that you will hopefully not need to resort to helicoiling.
Incidentally, both the bolts, and washers I supply are high tensile; with a 180K psi rating. I don't know what grade fasteners you were supplied - the minimum you should use for the mains are a grade 8, which is identified by six stripes on the head, and has a 150K psi rating. Grade 5 would only have 3 stripes and a 120K psi rating.
If these aren't even long enough, then have the areas of the strap where the bolt heads are spot-faced down by whatever length is needed, or machine the strap down. Note that if you do amchine the strap down, you might want to take approximately the same off each side if machining more than 20% of the original thickness off, otherwise you might find your strap will settle over time and do bad things by under, or over-clamping the cap...
Another point about washers - using the highest-strength super-whippy bolts is pointless if using 'putty steel' washers under the head. The highest contact stresses are directly under the bolt head, where the contact area is the smallest. Using washers of an insuficient grade will yield the surface of the washer, relieving the tension on the fastener. This is why it always takes less than 150lb ft to undo a crank bolt which has a locktab; the soft mild-steel tab has yeilded, relieving the bolt tension.
Potentially, you could be better running without washers; but is your strap a super-soft steel rather than an 8620 grade? I bet 99% are - which means you'll not retain the torque. The washers in my kit are designed to work with the fastener from the outset.
I'll supply the extra bolts and wahers free of charge as you seem to be in a bit of a pickle. These will be send priority in a few hours. You could likelly have them Saturday, if not Monday.
Regards,
Dave C
If you need any more help - I'm sure sprox will assist. He's not far away, and is one of few 'non trade' folks I'd ever trust to build me an engine.
Edited by turbodave, 16 June 2009 - 07:23 PM.
#45
Posted 16 June 2009 - 07:49 PM


The bolts i were given were grade 5, as they have 3 lines on the head of the bolt. So i would guess the straps made of poor steel aswell.
The solution you suggest sounds simple enough. When i took the block to be looked at, he ran a tap down the threads and screwed the bolt with good threads all the way down to check them. He said the threads are 42mm deep (or the hole for the bolt is that deep anyway, i assume its threaded all the way) and by looking at the bolt and down the threads with a torch, i'd say about 6mm of thread are stripped out.
Just been out and measured the strap, it does look to be slightly larger, its 1.2 inches tall. Still means the bolts i were supplied with were still way too short.
1 user(s) are reading this topic
0 members, 1 guests, 0 anonymous users