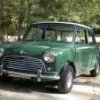
Drain Plug Threads - What Standard/form?
#16
Posted 15 February 2012 - 01:00 PM
Thank you for the kind comments :)
#17
Posted 18 February 2012 - 09:55 PM
#18
Posted 19 February 2012 - 08:02 AM
But the hex head head is definitely made to an exact fractional inch size, not the rather odd Whitworth, and if there is any attempt to adhere to the relevant BS standard, that would imply that the thread should be UNC.
I would also not extrapolate anything from what went before. Certainly the gear clusters in early Minis were derived from the A35 etc, but the casing was entirely new, and is also the engine sump, which on older vehicles was a steel pressing, so the sump plug, now with magnet, can be expected to be an entirely new part, and as the gearbox casing tooling must have been new, it would conform to the standards prevailing at the time, which were UNC/UNF.
Certainly early Morris Minors etc were Whitworth/BSF, and I have cannibalised bolts from some scrappers, invariably R grade, which was only used in Whitworth/BSF.
#19
Posted 19 February 2012 - 08:14 AM
#20
Posted 19 February 2012 - 04:13 PM
Whitworth must be recognized as a stronger design than a comparably sized UNC/UNF fastener. The root and crests of Whitworth threads have full radiuses to lower stress concentration and the 55 degree thread angle is lower to provide the ability to support more tensile stress than the 60 degree UNF/UNC profile. While not as strong as an ACME thread, Whitworth certainly has/had its use in high load applications.
That said, John's point about the sump plug thread is quite correct. The thread type of the sump plug with regard to its strength is rather moot when you consider the short length of engagement. Industry practice for threads in aluminum is to provide 1.5 times the diameter of thread engagement and that is not the case with the drain plug. The drain plug is an area where I choose to use a non-standard seal. Instead of the copper crush washer I use a bonded metal/rubber seal so almost no torque is required to seal the sump. Though I have installed HeliCoils in other people's Mini gearboxes I do not want to have to do this on my car.
#21
Posted 19 February 2012 - 08:34 PM
But looking at the threads, the pitch is the same in most Whitworth/UNC sizes (but not all, for some daft reason). Now Whitworth has a thread depth of 0.640327p, while UNC is 0.61344p on the male thread, which is the one which limits the strength on a correctly designed fastener. Also, the Whitworth root radius is 0.137324p, while UNC is 0.1443p. so UNC wins on stress raisers due to root radii again.
In this case, the strength is limited by the alloy casing, so normal bolting rules do not apply. But the information I have suggests that the female thread depth in UNC is 0.54127p, which is less than that of Whitworth, and because of the larger thread angle the actual thread form is wider so can withstand more shear load. But tightening up a steel bolt in a short soft alloy nut will cause plastic deformation of the nut, and the whole thing becomes remarkably complex to calculate, so I am not very convinced one way or the other.
Following normal bolting rules, where the liniting factor is the tensile strength of the bolt, the nut being made of the correct grade of material and with adequate engagement length, the figures say that UNC will be stronger, and UNF strongest.
#22
Posted 19 February 2012 - 09:05 PM
- Unfortunately to match the fatigue strength of a Whitworth thread you would need to use a UNJ, the simple facts are Whitworth had a controlled root radius thread form, wheras UN doesn't.
- THe strength of any fixing set is goverened by its weakest link, in some cases (no pun inteneded) its the bolt or male threaded part, in some ints the female part, in the case of the Mini gearbox its the female by deafault.
- A UNC (coarse) thread is better utilised in a coarse grained material such as aluminium or wood, and a fine or UNF is better used for brasses and steels.
- A fine thread in aluminium is rare because the designers are aware of this, in fact the only place I can think of is the 1/4"unf bolt that is the adjuster on Pre A+ clutch arms or the bracket support on later A+ models.
- Theory is a wonderful thing, but is always superceded by correct engineering techniques to make it work.
What I believe is that by doing the job correctly you only have to do it once !
I have seen M5 bolts used to hold the steering column to the rack, it very nearly resulted in a serious RTA, with unbearable consequences, the owner then told me he was selling, because the Mini is too dangerous !!
Now where do you draw the line ? The later Mini has M8 threads, well a UN 5/16" nut will fit an M8 bolt or stud, but again the consequences of this action is unthinkable.
People really need to stop and think about the actions they take before more Minis are written off due to stupidity and ignorance.
#23
Posted 19 February 2012 - 09:49 PM
Oh, and the UNC/UNF standards define certain limiting dimensions, but in practice the roots are almost always radiused, while still meeting the dimensional limits.
I don't doubt that if you put a plug with the wrong thread in, and tighten it, the ali thread will deform to match. and lose much of its fatigue life in the process. But if you keep using the same, wrong plug,and don't go mad with the torque,it will probably still last for umpteen oil changes. But tightening it up some more to overcome a worn and leaking washer may well lead to disaster.
An M5 on the steering column pinch bolt is the stuff of nightmares. I have to wonder about the person who did that. But I have seen other structural bodges, even on this forum, which are equally scary and less obviolus. Stainless bolts of unknown grade in highly inappropriate places, for example.
If we want to keep Minis on the road, as I am sure all forum members do, we should probably be finding ways of eliminating all the known weaknesses. If the sump plug is one of those, we should switch to using bonded seals, and just nipping the thing up with a short spanner, so there is no tendency to strip. The cost of repairing a stripped thread here is horrendous, because you can't just helicoil it in situ, as the sealing face needs to be accurately perpendicular to the thread axis, as you know. I would drill it out and weld in a machined insert, but you can't properly weld filthy, oily metal, so it might be an engine out and stripdown to fix it properly. Cost of materials negligible, labour many hundreds, which could result in some cars being written off. Best avoided.
#24
Posted 19 February 2012 - 11:00 PM
If we want to keep Minis on the road, as I am sure all forum members do, we should probably be finding ways of eliminating all the known weaknesses. If the sump plug is one of those, we should switch to using bonded seals, and just nipping the thing up with a short spanner, so there is no tendency to strip. The cost of repairing a stripped thread here is horrendous, because you can't just helicoil it in situ, as the sealing face needs to be accurately perpendicular to the thread axis, as you know. I would drill it out and weld in a machined insert, but you can't properly weld filthy, oily metal, so it might be an engine out and stripdown to fix it properly. Cost of materials negligible, labour many hundreds, which could result in some cars being written off. Best avoided.
100% agree
#25
Posted 19 February 2012 - 11:14 PM
AC
#26
Posted 20 February 2012 - 12:09 AM
And I am sorry but size for size, it is pretty well established that the Whitworth profile is stronger than UNC/UNF. If you insist... I'll dig up some engineering links online and post them here. The reason 60 degree UNC/UNF threads are here today has nothing to do with them being stronger. They only dominate the SAE fastener world because of WWII and the need for a common standard between the allies.
This thread (pun intended) had now drifted far away from its initial purpose. Above all else (and if nothing else) we all seem to agree that the sump plug really is a 5/8 UNC thread and for best results it must not be over-torqued. For some of us this is achieved by using bonded seals instead of the original copper washer.
#27
Posted 20 February 2012 - 08:28 AM
II have used 5/8" UNC for more than 15 years, never had a problem. Problems only arise when they are overtightened. Torque wrenches are made for a reason.
AC
That is also very true, although the tendency to "fix" a leak is to keep on tightening the part in question, a dowty washer is a very good way forward, or at the very least a new copper washer every time its removed, copper work hardens so every time it is retightened it loses some more of its sealing effects and unless you can anneal it yourself, replacement is best. A dowty washer doesn't need to be replaced after every oil drain and can continue to be used for years without failure.
#28
Posted 20 February 2012 - 09:30 AM
#29
Posted 20 February 2012 - 09:37 AM
#30
Posted 20 February 2012 - 10:58 AM
the simple question has turned into a "******* fight" and only now have we come to a conclusion that we should use a dowty washer instead of a copper washer and now thats going to turn into a fight over the size.
could we in future not turn questions into a " i have more knowledge than you" fight, a simple answer that we could understand will be better than the long drawn out technical answers given.
1 user(s) are reading this topic
0 members, 1 guests, 0 anonymous users