
Another Electric Mini
#46
Posted 08 September 2011 - 03:05 PM
Has it ever been on the road?
This year, at the Hillclimb and Sprint Association (hillclimband sprint.co.uk) sprint at Curborough we have a class specifically for electric vehicles. Be reallly nteresting to se something like thos there, but I guess it's range would mean a trailer is required.
#47
Posted 09 September 2011 - 09:53 AM
I need to get some time on a lathe to remake one of the stub shafts that carries the sprocket at one end, and the pot joint at the other. I made a mess of welding it up the first time and there's too much runout in the pot joint.
I've got most of the electrical components now. Can't afford the batteries and controller I really want right now, so I've decided to make do with what I've got just to get the mini on the road. I've robbed the motor controller from my electric motorcycle. This is an Alltrax 7245, with a maximum power output of just over 30 kW (about 40 hp). It should be enough for road testing anyway. The battery pack is made up of six or seven 42Ah lead acid batteries installed in the boot for a voltage of 72-84V. I've also robbed the lithium battery pack from my bike and may combine that with the lead acid cells to boost range to around 25 miles.
I still need to buy a couple more contactors. These are the heavy-duty DC relays needed to switch the power circuit. There's one for each motor, to reverse direction, and another set of three to switch the motors between series and parallel. Series/parallel switching is a way of maximising performance from a relatively low-power controller. In series mode you get maximum torque, for takeoff, and in parallel mode you get maximum speed, for cruising. Top speed won't be anything to shout about at this stage (50+ mph), but initial acceleration should be sprightly.
I would love to have a go at a hill climb once I've got a decent battery pack. Electric cars are well suited to an event like that, as you only need to carry enough batteries to last for a few minutes, and electric motors are generally much lighter than internal combustion engines. It's also possible to place the motors and batteries really low in the car to drop the centre of gravity, which is another advantage for racing.
#48
Posted 09 September 2011 - 01:15 PM

...Top speed won't be anything to shout about at this stage (50+ mph), but initial acceleration should be sprightly.
...still not exactly ridiculously slow.
I would love to have a go at a hill climb once I've got a decent battery pack. Electric cars are well suited to an event like that, as you only need to carry enough batteries to last for a few minutes, and electric motors are generally much lighter than internal combustion engines. It's also possible to place the motors and batteries really low in the car to drop the centre of gravity, which is another advantage for racing.
Electric motors also deliver all of their torque at anything over 0rpm, so you won't have to think about having the right gear (not really relevant in yours..), or finding the powerband.
#49
Posted 09 September 2011 - 02:13 PM
They still have a efficiency curve for power consumption if you are concerned about range.Sounds promising, but we need piiiiiiics!
...Top speed won't be anything to shout about at this stage (50+ mph), but initial acceleration should be sprightly.
...still not exactly ridiculously slow.
I would love to have a go at a hill climb once I've got a decent battery pack. Electric cars are well suited to an event like that, as you only need to carry enough batteries to last for a few minutes, and electric motors are generally much lighter than internal combustion engines. It's also possible to place the motors and batteries really low in the car to drop the centre of gravity, which is another advantage for racing.
Electric motors also deliver all of their torque at anything over 0rpm, so you won't have to think about having the right gear (not really relevant in yours..), or finding the powerband.
#50
Posted 10 September 2011 - 10:00 PM
have a few comments/ idea's
in the forklift world some makers run motors in series and parallel , low speed /turning use in series then switch to high/full speed use parallel - will need a few more contactors to make it happen tho ,
can/does the controller use regen - use the motors as generator for when braking or going down hill ?
one of the better things of using dc motors is the ability to deliver its full torque at very very low rpm -unlike a petrol / diesel engines , you may find the ratio / sprocket sizes can be much reduced or the running speed of the motors reduced ,
keep up the good work and keep the updates comming , good luck with it and hope to see it up and running .
#51
Posted 11 September 2011 - 09:34 AM
No, regen is difficult with series-wound motors like mine. It's fairly easy to do with permanent magnet or AC motors, but in most situations isn't as useful as you might think. You can't put the energy back into the batteries fast enough to gain much benefit in stop and go traffic, so you typically only gain a few per cent in efficiency. You would benefit more if you lived in a hilly part of the country, where there are long downhill stretches that call for steady braking. One way to improve regen is to use supercapacitors that act as a buffer between the motor and battery, but they're pricey and take up a lot of space.can/does the controller use regen?
#52
Posted 14 September 2011 - 09:22 AM
Would I be right in thinking you're an electrical engineer of some kind???
#53
Posted 14 September 2011 - 10:15 AM
No, I'm a welding engineer, though I haven't worked in the industry for a long time. I caught the EV bug a few years ago and have been reading up and asking electrical engineers stupid questions ever since.
I need to make time to acquire some CAD skills, as I could have saved myself a lot of head-scratching if I'd been able to model the mini subframe first. I hadn't given much thought to how I would enclose the chain drives, so the end result will be a bit untidy.
#54
Posted 15 September 2011 - 10:04 PM

One thing that's quite interesting is how exactly you did the inner driveshaft location bearings. Its sort of similar to my upper front subframe, where my suspension rockers will be mounted... Its a fabricated box section meeting a bit of tube that contains a bearing.. What bearing arrangement have you used (double row ball bearing??) and how was the bore affected by the welding?
On mine I mean where the orange bit goes through the white subframe...
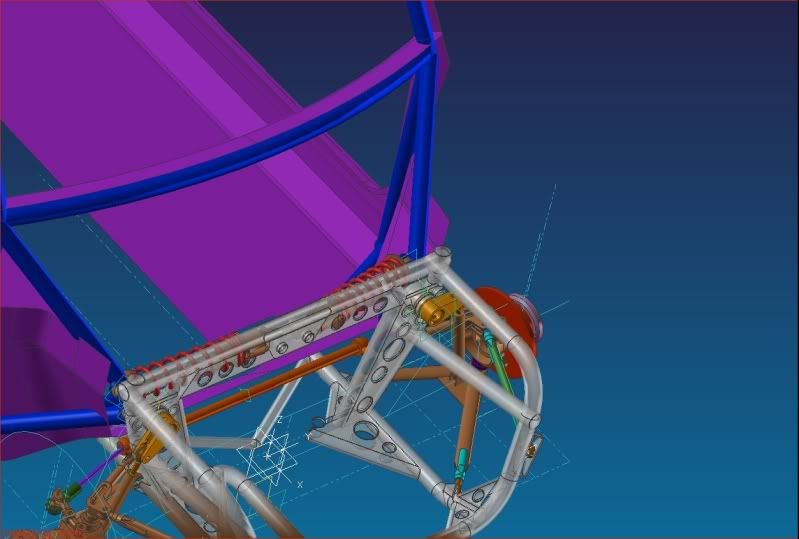
With yours - what are you thinking of in terms of a control system for the motors? Certainly with any conventional engine thats really the most important part of it, and from what little I know of electric vehicle technology it seems thats the same....... Mercedes Benz are designed the SLS hybrid drive system across the road from my work beleive it or not...

#55
Posted 16 September 2011 - 12:17 PM
I cheated and used kart axle bearing carriers designed for bearings with a spherical outer shell. This means they're self-aligning to some extent. Each stub shaft is supported by a ball bearing on either side of the box section. The carriers are also split across the diameter, so I can drop each stub shaft out from below. I don't have any machining facilities yet, so I'm trying to use off-the-shelf solutions where I can. Looks like you're doing it the proper way. That short length of tube that supports the rocker arm will be tricky to weld without distortion though. It would probably need reaming afterwards.


#56
Posted 16 September 2011 - 12:55 PM
I'd like to have a peek at how the big boys do it. They use AC drives, which require much more complex inverter controllers. The advantage of AC motors is that they don't have brushes and can spin at higher speeds. DC series wound motors, like I'm using, are generally cheaper and require much simpler controllers. Basically all the controller does is switch the power on and off very rapidly and varies the ratio of On time to Off time. The motors share current equally without any outside control.Mercedes Benz are designed the SLS hybrid drive system across the road from my work beleive it or not...
#57
Posted 22 September 2011 - 09:12 AM
Good idea with the go cart bearings - I guess we'll have to see how they handle the radial load as the torque you're going to generate will be quite a lot larger than in the usual application. With my rocker bearings, the current design has a machined housing which is welded into the fabricated structure but I am thinking it might be better to do something which bolts in to carry the bearings and therefore avoid the distortion problem...
Anyway - good luck with it and keep sticking up the photo's - looking forward to seeing this run.....
Dave.
#58
Posted 13 March 2012 - 06:52 PM
#59
Posted 15 March 2012 - 12:15 AM
I've started building the lithium pack and tidying up the existing electrics. Will post some photos soon.
#60
Posted 03 April 2012 - 08:13 PM
1 user(s) are reading this topic
0 members, 1 guests, 0 anonymous users