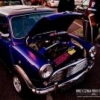
Hardening Crank?
#1
Posted 05 January 2009 - 01:36 AM
This is the spec so far.
998 a+
Swiftune SW10
Swiftune Duplex
Twin HS2'S Rebuilt by Burlen, Cooper 'S' Needles
Janspeed Inlet
ITG S/S Filter
n/a 12g940
Block Decked
1.27 forged 1275 Rockers
Maniflow LCB
Maniflow 1.75 single box
Aldon Yellow Dizzy
Lightend Dizzy Drive
Cross drilled, wedged, & knife edged Crank
Lightend, Polished & Shot Pean'd Rods + ARP bolts
MiniSport ultralight Flywheel
Orange Diaphragm
Eletric Fuel Pump
Rebuilt Gearbox by Heathrow Transmissions,
3.9FD, Centre Oil Pickup & KAD Quickshift.
Thanks.
#2
Posted 05 January 2009 - 10:49 AM
#3
Posted 05 January 2009 - 11:00 AM
my understanding is that if you have this done it could make it brittle and when under load could break. but i could be totally wrong. I think the other option is tuffrided. again could be wrong, but something to look at.
You'll probably find that they will go through a couple of different heat and cooling treatment processes to avoid it becoming brittle. For example they could harden and temper it then case harden it (Basically add carbon to the outer layer of metal 0.003mm) This makes it extremely hard but not britle.
#4
Posted 05 January 2009 - 12:47 PM
#5
Posted 05 January 2009 - 12:51 PM
I pesonally would save your money.
#6
Posted 05 January 2009 - 01:08 PM
#7
Posted 05 January 2009 - 01:11 PM
I think the sw10 is more suited to making big torque, it'd be great in a 1380 for example, with a 3.4 diff
No doubt it'll be good with an sw10, but i think you could do better with either a different cam like a 286, or you could have a lower diff, like something around a 3.6 to make use of the torque.
#8
Posted 05 January 2009 - 01:48 PM
Ah right, yeah I just brought the cam a couple of days back direct from them, Ive got a 3.6fd already sitting in there and a 3.44 lying around the garage somewhere, so overall id be better changing the fd to a higher one for better driveability?
Thanks for the advice everyone

with regards your spec, have you got your sw10 already? Its a very good cam, and pulls strong low down, but i dont think it'd be suited to a 3.9 final drive really. I had an sw10 in a 1071 with a 3.9 diff and whilst it was a lot of fun in 1st and 2nd (it'd do 9000rpm in first) It really lacked power to pull it up the rev range once you got into 4th or even 3rd. IIRC it'd get to about 6000 in 4th before struggling.
I think the sw10 is more suited to making big torque, it'd be great in a 1380 for example, with a 3.4 diff
No doubt it'll be good with an sw10, but i think you could do better with either a different cam like a 286, or you could have a lower diff, like something around a 3.6 to make use of the torque.
#9
Posted 05 January 2009 - 05:44 PM
didnt realise that it was just a different name for case hardening.
It's not and neither is Nitriding. They're different forms of surface hardening in so much as the hardening that is applied is a specific chemical compound applied in a different way but the effect it similar to case hardening, although more advanced. Tuftriding is a patented process owned by one of the big chemical companies (DuPont or ICI I think). Also I don't think many engineers actually offer real Tuftriding any more because it's pretty dangerous and has huge health and safety implications in a plant. The Tuftriding liquid is made of many different Cyanide compounds in a big heated bath that you drop cold items into. Pretty dangerous and I believe that it's actually done in just a few places so your local shop will send things away to be done and you might not get parts back for some time. The modern equivalent is Nitriding and this is much more effective, providing a thicker finish and with less danger of warping the item being treated. Nitriding is applied to heated parts in a vacuum and is similar to the way that metals are lifetime oiled in various precision machines such as motion picture cameras. Nitriding is better, thicker and longer lasting than Tuftriding but each is more effective on a different range of metals I believe.
#10
Posted 06 January 2009 - 01:04 AM
didnt realise that it was just a different name for case hardening.
It's not and neither is Nitriding. They're different forms of surface hardening in so much as the hardening that is applied is a specific chemical compound applied in a different way but the effect it similar to case hardening, although more advanced. Tuftriding is a patented process owned by one of the big chemical companies (DuPont or ICI I think). Also I don't think many engineers actually offer real Tuftriding any more because it's pretty dangerous and has huge health and safety implications in a plant. The Tuftriding liquid is made of many different Cyanide compounds in a big heated bath that you drop cold items into. Pretty dangerous and I believe that it's actually done in just a few places so your local shop will send things away to be done and you might not get parts back for some time. The modern equivalent is Nitriding and this is much more effective, providing a thicker finish and with less danger of warping the item being treated. Nitriding is applied to heated parts in a vacuum and is similar to the way that metals are lifetime oiled in various precision machines such as motion picture cameras. Nitriding is better, thicker and longer lasting than Tuftriding but each is more effective on a different range of metals I believe.
Had to dig out my old college books for this one,quite intresting.
all the terms come under 'the surface hardening of steels'.
The book refers to case-hardening for low carbon steels by adding carbon to the surface 'carburising'
Tuftriding is not mentioned but it does discribe the process and referes to it as 'carburising in liquid media, liquid carburising or cyanide carburising' containing sodium cyanide and sodium carbonate. so yer tuftriding must be a trade name.
Tuftriding is carburising and as such case hardening.
Nitriding again is surface hardening, but differs from the above as it is for special steels 'Nitralloy steels' these steels contain aluminium, chromium, vanadium and molybdenum, but it does discribe it as used on crankshafts.
There are loads of surface hardening discribed in this book, another one mentioned for cranks is ionitriding.
I think the reason for classing Tuftriding/carburising as 'case harding' is the process adds carbon to the outer surface allowing the surface to be hardened by the time old heating and quenching of the item. But Nitriding is classed as surface hardening, as the process forms a hard surface of nitrogen aluminium chromium and vanadium, it is done after machining at quite low temp and less lightly to crack or distort the item.
As you said ,looks like you need to find out what surface hardening is best suited to the crank matreial or it will not work and you waste your money.
Edited by rozzer1275, 06 January 2009 - 01:36 AM.
1 user(s) are reading this topic
0 members, 1 guests, 0 anonymous users