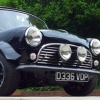
Stripped Centre Main Thread!
#1
Posted 13 June 2009 - 09:12 PM
So i clean the new bearings, slot them in, oil them up, drop the crank in. Put my new thrust washers in and the crank had no end float at all, not even the thinnest feeler gauge i had would fit. So i cleaned up the old ones and slotted them in and got 4 thou endfloat, so good enough the hanyes tell me. I don't know if thats bad practice or what but its better than having no end float there at all, right?
Anyway thats not the problem. I put more oil on the journals/cap bearing, put the cap on, put the centre main strap on. Get the bolts out, loads of oil on the threads, oil on the face of the strap and screw them in.
The bolts went in fine made a good few turns by finger, i could tell the bolt was engaged ok in the thread. So i got the spanner out and carried on screwing them in until they touched the main strap. They didn't take alot of pressure at all, barely anything, nothing to say there was anything wrong with the threads.
So they come into contact, i get the torque wrench out set it to 63fb/lbs, bring one bolt down, the cranks still nice a free/smooth. Bring the other bolt down, feel a clunk rather than a click of the torque wrench, the feel the wrench go slack!
I grab the bolt, it lifts straight out with no thread left on it at all! I tryed another bolt in the block and that won't screw in.
So basically i've stripped the thread in the block!!
Is this something that can be helicoiled?
I'm doubting my ability to build this engine now, i've lost my enthusiasm for the whole thing! If it turns out the block scrap i'm screwed, i've just spent all my moeny on parts for this new build, i can't afford a new block!
#2
Posted 13 June 2009 - 09:26 PM
Well i get home from work, find my internets broke. So decide to go and make a start on my engine. I'm following this engine builder DVD to the word!
So i clean the new bearings, slot them in, oil them up, drop the crank in. Put my new thrust washers in and the crank had no end float at all, not even the thinnest feeler gauge i had would fit. So i cleaned up the old ones and slotted them in and got 4 thou endfloat, so good enough the hanyes tell me. I don't know if thats bad practice or what but its better than having no end float there at all, right?
Anyway thats not the problem. I put more oil on the journals/cap bearing, put the cap on, put the centre main strap on. Get the bolts out, loads of oil on the threads, oil on the face of the strap and screw them in.
The bolts went in fine made a good few turns by finger, i could tell the bolt was engaged ok in the thread. So i got the spanner out and carried on screwing them in until they touched the main strap. They didn't take alot of pressure at all, barely anything, nothing to say there was anything wrong with the threads.
So they come into contact, i get the torque wrench out set it to 63fb/lbs, bring one bolt down, the cranks still nice a free/smooth. Bring the other bolt down, feel a clunk rather than a click of the torque wrench, the feel the wrench go slack!
I grab the bolt, it lifts straight out with no thread left on it at all! I tryed another bolt in the block and that won't screw in.
So basically i've stripped the thread in the block!!
Is this something that can be helicoiled?
I'm doubting my ability to build this engine now, i've lost my enthusiasm for the whole thing! If it turns out the block scrap i'm screwed, i've just spent all my moeny on parts for this new build, i can't afford a new block!
Yes it can be helicoiled. Used to do this all the time when I used to build Leyland train engines!
#3
Posted 13 June 2009 - 09:45 PM

So can pretty much any machine shop/engineering place do helicoiling now? Its not a specialist thing is it?
#4
Posted 13 June 2009 - 10:39 PM
What worries me is that you say you needed to use a spanner, howver slight, to screw the bolts in. These bolts should go ALL the way in with light finger pressure, if they dont, there is something wrong, and you need to find out why, before you go any further.
Other things to consider, the torque setting is for dry threads, not oiled, adn how acurate is your torque wrench anyway, has it been calibrated? I wouldnt consider building any engine using an un tested torque wrench

#5
Posted 13 June 2009 - 10:51 PM
If there is no thread on the bolt, it is clearly still in thethread in the block. if the thread in the block is ok, it might just need cleaning out with a tap. The bolts on these center mains straps are very well known to be the wrong grade for the aplication most are using them for.
What worries me is that you say you needed to use a spanner, howver slight, to screw the bolts in. These bolts should go ALL the way in with light finger pressure, if they dont, there is something wrong, and you need to find out why, before you go any further.
Other things to consider, the torque setting is for dry threads, not oiled, adn how acurate is your torque wrench anyway, has it been calibrated? I wouldnt consider building any engine using an un tested torque wrench
Well there is probably 3 or 4 threads missing off the centre main bolt, when i say missing, its almost like a shouldered bolt now and there was bits of thread and fragments stuck to it. Don't know if those threads were off the bolt itself or from inside the block. All i know is, the bolt lifted straight out of the hole in the block, as there are no threads left on the bolt and I have tried screwing another new centre main bolt into the block, but they won't screw in at all.
So basically the thread in the block is also damaged.
The torque wrench is brand new. I bought a brand new teng tools wrench specially for building this engine properly, came with a callibration certificate.
So if the torque wrench settings are for dry bolts, is there a set percentage i should increase/decrease the torque settings by?
Bill Sollis on the engine DVD, said to oil all the bolts up so it doesn't give a false reading of friction. He also said centre main bolts should be 68ft/lbs; but my haynes said 63ft/lbs. So I went with the haynes rating.
The bolt went in by hand a good 4-5 full turns really smoothly, it was engaged in the thread as it couldn't be pulled out. It did get a little too stiff to do by hand, which is when i switched to the spanner, but the spanner took no effort at all, i was pretty much just spinning the spanner round with my finger.
#6
Posted 13 June 2009 - 11:20 PM
you say you have a cetre main strap... there are a of certre main strap kits being supplied with rubish quality bolts (sprocket will confirm that

i would sugest you have a look down the offending hole, and see if the threads left in there from the bolt will puul/peel out with a pair of pliers/tweezers to leave a thread thet looks ok, if so clean the tread up with a tap, and see how it looks, if it looks ok get a couple of bolts from a guy on ebay that sell them (also sells ally timing plates and gearbox to engine bolts)
#7
Posted 13 June 2009 - 11:34 PM
I'll have a look tommorow and see what the threads are like in the block. When you try and screw a bolt in now, it feels as though there is still some thread there and that its trying to thread in, but doesn't seem to get there without getting stiff when turning by hand.
i'll try and clean them up and see whats left in the block.
I've had a quick look on ebay, the only uprated main strap bolts i can find are these: Link
From america, which means i could be waiting a while for postage...
#8
Posted 14 June 2009 - 12:09 AM

Is the starp a 1" square or is it 1x1/2"? I think those bolts are only for the 1" square straps
You will need a 7/16" UNF tap to try and clean the threads up. Dont go mad with it, be gentle otherwise you can cut the threads out of the block which might actualy be recoverable
If you do need to get it helicoiled, I can recommend The Headshop UK in Warrington. Not the closest machine shop to you, but, they are the only guys I would trust to take some care over it.
#9
Posted 14 June 2009 - 08:59 AM
If not i'll give the headshop a ring. Don't mind travelling if its worth the drive. Infact, i'm going to liverpool on monday so will be passing warrinton...
#10
Posted 14 June 2009 - 11:18 AM
I suspect the threads in the block will be ok, fingers crossed

#11
Posted 14 June 2009 - 11:33 AM
#12
Posted 14 June 2009 - 02:26 PM
Helicoils are totally acceptable. In fact, on the alloy blocks of aircraft engines, all threads have to be helicoiled for safety.
For the sake of a few quid for helicoiling it's not worth the risk.
#13
Posted 14 June 2009 - 04:29 PM
I would not take the risk with the threads on such a critical application. It would be advisable to helicoil it for the sake of safety. Remember, if the thread 'lets-go' under high load, it will take out the crank, block and gearbox.
Helicoils are totally acceptable. In fact, on the alloy blocks of aircraft engines, all threads have to be helicoiled for safety.
For the sake of a few quid for helicoiling it's not worth the risk.
Don't forget that helicoiling which is basically increasing the thread size (bigger hole) will diminish the amount of material left to support the main cap, therefore be very careful about helicoiling the main cap bolt / stud holes

#14
Posted 14 June 2009 - 04:34 PM
Going to have a look at the threads later on...
#15
Posted 14 June 2009 - 05:33 PM
I would not take the risk with the threads on such a critical application. It would be advisable to helicoil it for the sake of safety. Remember, if the thread 'lets-go' under high load, it will take out the crank, block and gearbox.
Helicoils are totally acceptable. In fact, on the alloy blocks of aircraft engines, all threads have to be helicoiled for safety.
For the sake of a few quid for helicoiling it's not worth the risk.
Don't forget that helicoiling which is basically increasing the thread size (bigger hole) will diminish the amount of material left to support the main cap, therefore be very careful about helicoiling the main cap bolt / stud holes
So you mean my cap and strap will have to be drilled out and a bigger bolt fitted? I thought the whole idea of a helicoil was to avoid that? All the helicoils i've seen retain the original thread size.
Anyway i've been out with the tweezers and a torch and I can clearly see that after the first couple of threads, there is a section of 3-5 threads missing.
There are a couple of small fragments of thread in there, which i've removed, but still no joy with screwing the bolts in.
So looks like i've really done a fair bit of damage to the thread in the block.
So basically, my only option is helicoiling right? Am i best leaving it to a machine shop? There kits on ebay in the correct thread for £25: Link
I'd rather get it done professionally anyway really, providing its not rediculously expencive.
So the head shop UK you say sproket? Is this the place: http://www.astonmartinparts.co.uk/
1 user(s) are reading this topic
0 members, 1 guests, 0 anonymous users